Industrial gas purity testing is crucial for industries such as pharmaceuticals, food and beverage, aerospace, and manufacturing, where gases play a pivotal role in production, sterilization, and other critical applications. Ensuring that industrial gases meet the required purity levels is essential for maintaining product quality, regulatory compliance, and operational safety. However, there are several challenges in gas purity testing that can impact the accuracy and reliability of results. In this blog, we’ll explore the 10 key challenges in industrial gas purity testing and provide insights on how to overcome them.
Challenge 1: Variability in Gas Composition
One of the most common challenges in industrial gas purity testing is the natural variability in gas composition. Industrial gases, such as oxygen, nitrogen, or carbon dioxide, can have different purity levels depending on the source, production methods, and handling procedures.
How to Overcome: Implement routine testing at multiple points within the gas supply chain to ensure consistent quality. Use high-quality gas sources and ensure proper storage and handling procedures to minimize contamination. Calibration of testing equipment is also crucial to account for any fluctuations in gas composition.
Challenge 2: Sampling Methodology and Contamination
The way gas samples are taken can significantly affect the accuracy of industrial gas purity testing. Contaminants introduced during the sampling process—such as from unclean containers, improper handling, or leaks—can lead to inaccurate results.
How to Overcome: Develop standardized sampling protocols that minimize the risk of contamination. Use clean, well-maintained sampling equipment, and ensure that gas containers and lines are free of contaminants. In addition, perform tests as quickly as possible after sampling to reduce the likelihood of contamination during transport.
Read More: What You Need to Know About Compressed Air Testing: A Comprehensive Guide
Challenge 3: Inadequate Calibration of Testing Equipment
Calibration errors in testing equipment can lead to inaccurate measurements of gas purity. If gas analyzers or sensors are not properly calibrated, the results of purity tests may not reflect the true composition of the gas.
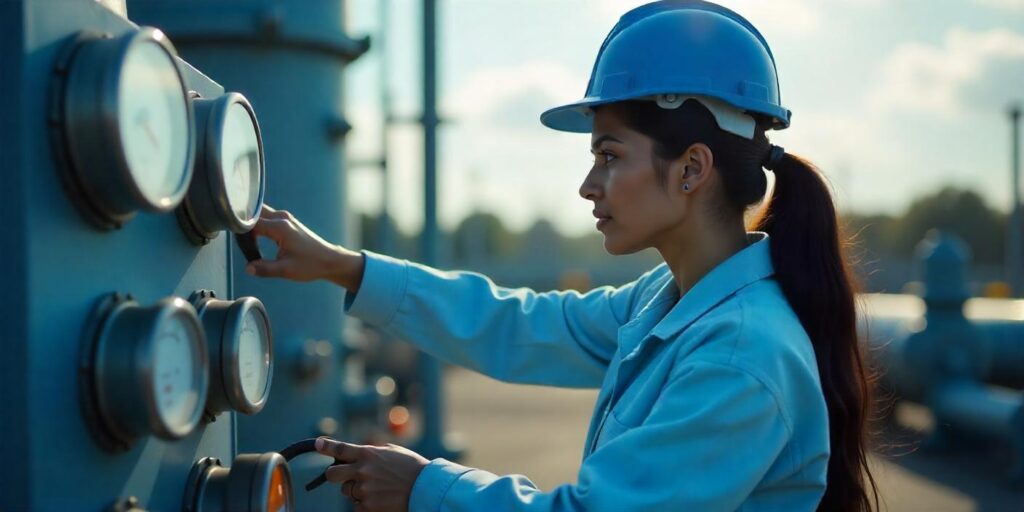
How to Overcome: Regularly calibrate all testing equipment according to the manufacturer’s specifications and industry standards. Create a calibration schedule and keep thorough records to ensure that equipment is functioning correctly and providing accurate results.
Challenge 4: Sensitivity of Detection Methods
Different gases require different methods of detection, and some testing methods may lack the sensitivity required to detect trace impurities. Inaccurate or insufficiently sensitive methods can lead to erroneous conclusions about gas purity.
How to Overcome: Use advanced detection technologies, such as gas chromatographs or mass spectrometers, that are specifically designed for the gas being tested. Regularly evaluate and upgrade testing methods to keep pace with advancements in detection technology and improve sensitivity.
Challenge 5: Pressure and Temperature Variations
Gas purity can be affected by changes in temperature and pressure, both during the sampling process and within the testing equipment. Variations in these parameters can lead to discrepancies in gas measurements.
How to Overcome: Ensure that industrial gas purity testing is done under controlled temperature and pressure conditions. Monitor and regulate these parameters during both the sampling and testing phases to minimize variability. Using temperature and pressure compensation techniques can help account for changes during testing.
Read More: Seal Strength Testing: Importance, Standards, Protocols, and Advanced Considerations
Challenge 6: Gas Storage and Distribution Contamination
Gases may pick up contaminants from storage tanks, pipelines, or distribution systems. If the gas is exposed to air, moisture, or particulates during storage or transportation, the purity levels may be compromised by the time it reaches the testing stage.
How to Overcome: Regularly inspect and maintain gas storage and distribution systems to ensure they are free from contaminants. Use high-quality gas cylinders and ensure that pipelines are adequately cleaned and maintained to prevent contamination of the gas.
Challenge 7: Regulatory Compliance and Standards
Meeting regulatory requirements for gas purity can be challenging due to the variety of standards and regulations that may apply depending on the industry and location. Regulatory changes can make it difficult to keep up with compliance requirements and maintain appropriate testing protocols.
How to Overcome: Stay updated on relevant industry regulations and standards, such as those from the FDA, ISO, or OSHA, that apply to gas purity testing. Work closely with regulatory bodies to ensure your testing processes are always in compliance. Develop an internal audit system to verify that all testing procedures meet regulatory requirements.
Read More:Master the A-Z of Disinfectant Efficacy Testing: Now Achieve Clean Pharmaceutical Environments
Challenge 8: Limited Access to Advanced Testing Technologies
In some cases, limited access to sophisticated testing technologies, such as gas chromatographs or mass spectrometers, can hinder the ability to perform accurate and comprehensive purity tests.
How to Overcome: Invest in modern testing technologies to improve the accuracy and scope of your industrial gas purity testing. Consider partnering with testing laboratories that have access to advanced equipment, or collaborate with research institutions to stay up to date on the latest technologies.
Challenge 9: Real-Time Monitoring and Data Analysis
Real-time monitoring of gas purity is critical in many industries to ensure that gas quality is consistently maintained. Without an efficient system for real-time data collection and analysis, companies may miss out on important trends or deviations in gas purity.
How to Overcome: Implement real-time gas monitoring systems that provide continuous data on purity levels. Use automated data collection and analysis tools to detect anomalies and trends quickly. This will allow for prompt corrective actions before the gas purity deviates beyond acceptable limits.
10. Challenge 10: Lack of Skilled Personnel
Gas purity testing requires specialized knowledge and expertise to interpret test results accurately. A lack of skilled personnel or insufficient training can result in incorrect testing procedures, misinterpretation of results, and inaccurate conclusions.
How to Overcome: Invest in continuous training and development programs for staff involved in gas purity testing. Ensure that your personnel are well-versed in the latest testing methods, regulatory requirements, and technologies. Consider hiring experienced professionals or partnering with third-party laboratories for expert support.
Conclusion
Industrial gas purity testing is a complex process that requires attention to various factors, including sampling methods, equipment calibration, environmental conditions, and regulatory compliance. By understanding and addressing these challenges, you can ensure that your gas purity testing is accurate, reliable, and compliant with industry standards.
How Prewel Labs Can Help
At Prewel Labs, we provide comprehensive industrial gas purity testing services to help you overcome these challenges and ensure the highest levels of gas quality. Here’s how we can support you:
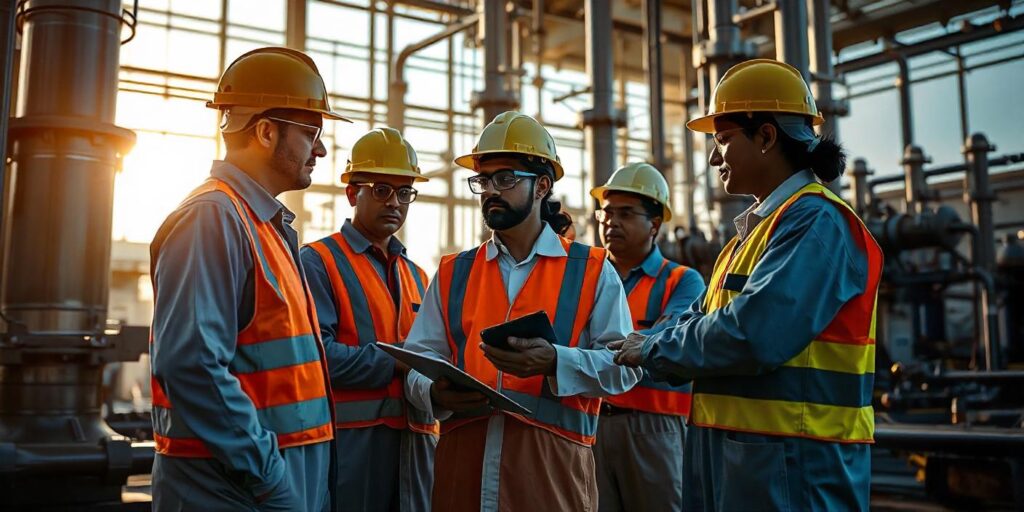
- Expert Testing: Our team uses advanced technologies and expertise to perform accurate and reliable gas purity tests, ensuring your gases meet regulatory standards.
- Calibration and Maintenance: We offer calibration and maintenance services for testing equipment, ensuring that your instruments provide accurate results every time.
- Regulatory Compliance: We stay updated on industry regulations and ensure that all gas purity testing is fully compliant with the relevant standards.
- Real-Time Monitoring: Our real-time monitoring systems allow you to track gas purity continuously, ensuring early detection of any deviations from the desired purity levels.
Partner with Prewel Labs for precise, reliable, and compliant industrial gas purity testing. Contact us today to learn more about our services and how we can help ensure the purity of your industrial gases
Authors
-
Surendra is an Assistant Manager in the Utility Testing Department with over 8 years of experience in steam, compressed air, and industrial gas purity testing. He has worked with leading testing service providers, including SGS, and has conducted on-site testing for top manufacturing, pharmaceutical, and food & beverage industries such as Merck, Biocon, Coca-Cola, and many others. Passionate about quality and compliance, he shares technical insights to help industries maintain optimal utility standards.
View all posts -
With an abundance of experience in the field of SEO, Adithya is someone who is curious about the domain. He has published over 700 articles under his name and has worked for companies like EssentiallySports, TCS, and more.
View all posts -
Arjun Jha has over 8 years of experience in tech startups, business strategy, and digital and traditional marketing. He’s helped many startups grow by using creative strategies and a deep understanding of the market. Outside of work, Arjun enjoys reading about business, philosophy, psychology, and spirituality, which inspires his unique approach to problem-solving and growth.
View all posts