Disinfectant efficacy testing (DET) is integral to maintaining cleanroom hygiene and ensuring compliance in pharmaceutical and biotechnology facilities. While much attention is given to the microbial efficacy of disinfectants, one critical aspect often overlooked is surface compatibility. Ensuring that a disinfectant is compatible with the surfaces it will be applied to is quite vital for maintaining equipment integrity, operational efficiency, and long-term cleanroom performance.
This blog explores why surface compatibility is a key factor in Disinfectant efficacy testing, its implications for pharmaceutical and biotech facilities, and best practices for incorporating surface compatibility assessments into your contamination control strategies.
Why Surface Compatibility Matters
Surface compatibility in Disinfectant efficacy testing refers to the ability of a disinfectant to perform its intended function without damaging the surfaces it is applied to. This aspect is crucial because:
- Material Integrity: Prolonged or repeated exposure to incompatible disinfectants can corrode, discolor, or degrade surfaces such as stainless steel, glass, polymers, and coatings.
- Operational Efficiency: Damage to critical surfaces or equipment can lead to operational downtime and increased maintenance costs.
- Regulatory Compliance: Regulatory bodies like FDA and EMA expect comprehensive validation of cleaning protocols, including the assurance that disinfectants do not compromise cleanroom surfaces.
- Product Safety: Surface damage can lead to contamination risks, such as leaching of degraded materials or harboring microorganisms in cracks and crevices.
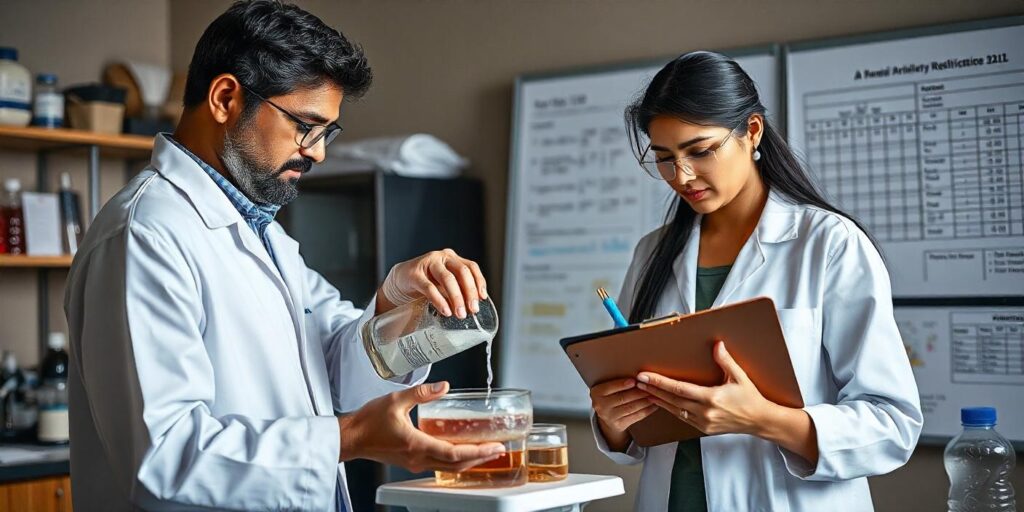
Real-World Applications of Surface Compatibility in DET
1. Cleanroom Walls and Floors
Cleanroom surfaces are subjected to regular disinfection to maintain microbial control. Testing the compatibility of disinfectants with epoxy coatings, vinyl tiles, and other common materials ensures long-term durability and cleanliness.
Example: A biotech facility evaluated a new hydrogen peroxide-based disinfectant and found it caused discoloration on their epoxy-coated floors. By identifying this issue during DET, they avoided widespread damage and opted for an alternative disinfectant.
2. Stainless Steel Equipment
Stainless steel is widely used in pharmaceutical manufacturing due to its durability and resistance to corrosion. However, certain disinfectants, such as those with high chloride content, can lead to pitting corrosion.
Example: A vaccine manufacturer tested a chlorine-based disinfectant on their stainless-steel bioreactors and observed signs of corrosion. Switching to a peracetic acid-based disinfectant preserved the integrity of their equipment.
Read More: 5 New Cutting-Edge Technologies in Disinfectant Efficacy Testing
3. Plastic and Polymer Surfaces
Polymeric materials used in cleanroom furniture, tubing, and isolators can degrade when exposed to harsh chemicals. Compatibility testing prevents cracking, discoloration, or loss of structural integrity.
Example: A pharmaceutical company performing aseptic filling validated that their disinfectant did not cause cracking in polycarbonate isolators, ensuring a sterile environment for production.
4. Glass and Optical Components
Glass surfaces, including windows and optical sensors, are susceptible to etching or fogging when exposed to incompatible disinfectants. Testing ensures clarity and functionality are maintained.
Example: A diagnostics company discovered that their disinfectant left residues on optical sensors, interfering with readings. Adjusting the formulation resolved the issue without compromising efficacy.
5. Specialized Coatings and Finishes
Certain cleanrooms utilize anti-static or antimicrobial coatings. Surface compatibility testing ensures these specialized finishes retain their properties post-disinfection.
Example: A pharmaceutical packaging unit validated that their anti-static flooring remained effective after repeated applications of an alcohol-based disinfectant.
Best Practices for Surface Compatibility Testing
- Early Assessment: Integrate surface compatibility tests during the disinfectant selection process to identify potential issues early.
- Material-Specific Testing: Test disinfectants on all materials present in the cleanroom, including walls, floors, equipment, and furnishings.
- Simulate Real-World Conditions: Conduct tests under conditions that mimic actual usage, including contact time, concentration, and frequency of application.
- Document Observations: Record physical changes such as discoloration, corrosion, or residue formation to guide decision-making.
- Collaborate with Vendors: Work with disinfectant manufacturers to understand product limitations and gain recommendations for compatible materials.
Read More: 6 Mindsets That Could Derail Your Disinfectant Efficacy Testing Results
How Prewel Labs Can Help
Prewel Labs offers a comprehensive suite of disinfectant efficacy testing services, including surface compatibility assessments tailored to the unique needs of pharmaceutical and biotech facilities. Our services include:
- Material Compatibility Testing: Evaluating the impact of disinfectants on a variety of materials and surfaces.
- Customized Protocols: Designing tests that reflect your facility’s specific cleaning practices and environmental conditions.
- Regulatory Support: Providing detailed, audit-ready documentation to satisfy regulatory requirements.
- Expert Consultation: Offering insights and recommendations to optimize your contamination control strategies.
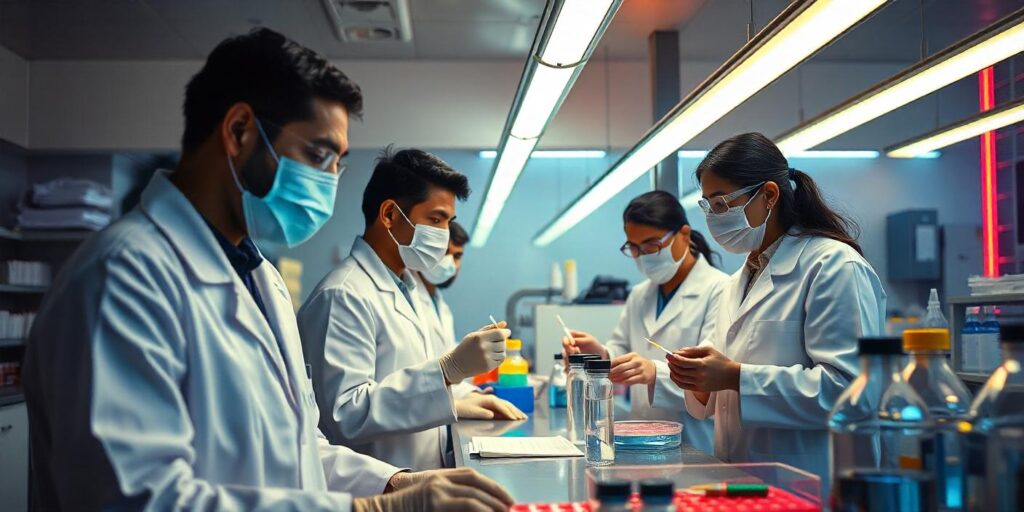
By partnering with Prewel Labs, you can ensure that your disinfectants are both effective and compatible, preserving the integrity of your cleanroom and equipment.
Conclusion
Surface compatibility is a crucial yet often underappreciated aspect of disinfectant efficacy testing. By ensuring that disinfectants work harmoniously with cleanroom materials, facilities can avoid costly damage, maintain regulatory compliance, and uphold the highest standards of contamination control. With the expertise of Prewel Labs, you can confidently integrate surface compatibility into your Disinfectant efficacy testing protocols, safeguarding both your operations and your products.
Authors
-
With over 20 years of experience in the pharmaceutical sector, Kumar Swamy M V is a seasoned expert in Quality Control Microbiology. Holding a Master’s degree in Microbiology, he has built a distinguished career across notable organizations, including Syngene, Biomed, Hikal, Apotex, and Cipla. His extensive industry knowledge spans various regulatory standards, such as USFDA, MHRA, ANVISA, and WHO, making him a trusted authority in compliance and audit
View all posts -
Arjun Jha has over 8 years of experience in tech startups, business strategy, and digital and traditional marketing. He’s helped many startups grow by using creative strategies and a deep understanding of the market. Outside of work, Arjun enjoys reading about business, philosophy, psychology, and spirituality, which inspires his unique approach to problem-solving and growth.
View all posts -
With an abundance of experience in the field of SEO, Adithya is someone who is curious about the domain. He has published over 700 articles under his name and has worked for companies like EssentiallySports, TCS, and more.
View all posts