Pure steam plays a vital role in various industries, particularly in the pharmaceutical, biotechnology, and food processing sectors. Its applications range from sterilization to heating and energy generation. However, ensuring the purity and quality of steam is crucial for maintaining product integrity, ensuring compliance with industry regulations, and optimizing operational efficiency. This comprehensive guide will walk you through everything you need to know about pure steam quality testing, including its importance and the methods of pure steam quality testing.
What is Pure Steam and Why is Pure Steam Quality Testing Important?
Pure steam refers to steam that is free of impurities such as dissolved solids, minerals, or organic contaminants. It is produced by vaporizing water in a controlled environment and is often used in processes that require high levels of cleanliness, such as sterilization in pharmaceutical manufacturing or in the preparation of high-purity water for injection (WFI).
Testing the quality of pure steam is critical for several reasons:
-
- Sterility Assurance: In industries like pharmaceuticals and biotechnology, pure steam is used for sterilizing equipment, vessels, and materials. Any impurities can compromise the sterilization process, potentially leading to contamination.
-
- Operational Efficiency: Impurities in steam can cause corrosion in equipment, leading to failures, maintenance costs, and operational downtime. Ensuring pure steam quality helps optimize the lifespan of equipment and ensures smooth operations.
-
- Product Quality: In industries like food and beverage manufacturing, where pure steam is used for heating or cooking, impurities can affect the taste, appearance, and safety of the end product.
Key Parameters in Pure Steam Quality Testing
In pure steam quality testing, temperature and pressure play a critical role. Monitoring these parameters ensures that pure steam remains in its gaseous form, vital for effective sterilization and heating processes.
The parameters in pure steam quality testing illustrate the importance of maintaining high standards for steam purity. Regular testing is essential in achieving the required levels of pure steam quality testing.
To ensure pure steam consistently meets industry standards and is suitable for its intended use, several key parameters must be carefully monitored and tested. These parameters are critical in guaranteeing that the steam maintains the necessary purity, efficiency, and safety for high-precision applications, particularly in regulated industries such as pharmaceuticals, biotechnology, food processing, and healthcare. Below is an in-depth look at the primary parameters involved in pure steam quality testing.
1. Temperature and Pressure
Pure steam is typically generated at high temperatures and pressures to ensure it is in its gaseous form without the presence of liquid water. The thermal properties of pure steam directly impact its performance in sterilization and heating applications. The temperature and pressure of steam must be precisely controlled and monitored to ensure it behaves according to its required specifications.
-
- Sterilization Processes: Steam is often used for sterilization in pharmaceutical manufacturing and medical device processing. The temperature must be high enough to ensure that all microorganisms are killed, but it should not be too high to cause degradation of equipment or materials. For instance, autoclaves, which are commonly used in sterilization, typically operate at temperatures between 121°C (250°F) and 134°C (273°F).
-
- Process Control: In industries like food and beverage processing or chemical manufacturing, steam is used for heating or maintaining temperatures in reactors and heat exchangers. Monitoring the pressure ensures that the steam remains in a superheated state, allowing it to transfer heat efficiently without condensation.
Testing Temperature and Pressure
Temperature and pressure are typically monitored using sensors that provide continuous feedback to ensure the system operates within the required ranges. Both must be maintained within specific limits to avoid excessive moisture formation, contamination, or the formation of non-condensable gases.
2. Moisture Content
Impact of Moisture on Steam Quality
Moisture in steam is one of the most significant contaminants that can affect its performance and the overall quality of the steam system. When steam contains excessive moisture (water droplets), it can cause problems such as:
-
- Corrosion: Moisture can cause corrosion in pipes, valves, and equipment, particularly in pharmaceutical and food processing facilities where any corrosion could lead to contamination of the product.
-
- Inefficiency in Sterilization: In sterilization processes, moisture can compromise the effectiveness of steam, as wet steam does not efficiently transfer heat to the surfaces that need to be sterilized. This can lead to incomplete sterilization, risking the contamination of sensitive products.
-
- Energy Loss: Wet steam has lower thermal energy than dry steam, making it less efficient for heat transfer applications. This can increase operational costs and affect system efficiency.
Testing Moisture Content
Moisture content is typically measured using moisture analyzers that detect the amount of liquid water in the steam. These analyzers use different techniques, such as gravimetric methods, infrared sensors, or capacitance measurements, to provide accurate moisture content readings. It’s critical to test moisture levels regularly to ensure the steam remains within acceptable limits, typically less than 0.5% moisture for high-quality steam used in pharmaceutical applications.
3. Non-Condensable Gases
Why Non-Condensable Gases Are a Concern
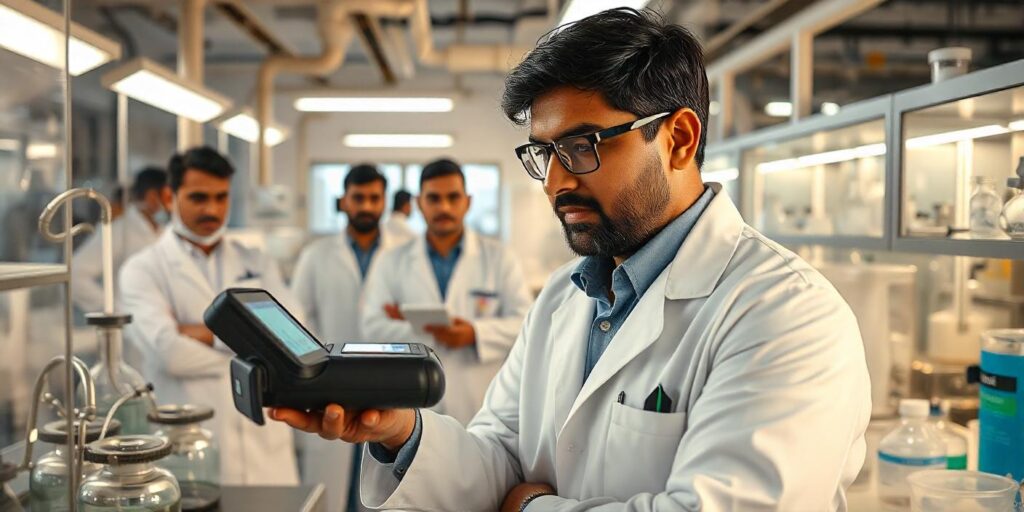
Non-condensable gases, such as air, nitrogen, carbon dioxide, and oxygen, can contaminate steam systems and disrupt their efficiency. These gases do not condense with steam and can create issues such as:
-
- Sterilization Inconsistencies: Non-condensable gases can interfere with the steam’s ability to uniformly heat surfaces, leading to uneven sterilization in critical applications like autoclaves and pharmaceutical sterilization chambers.
-
- Heat Transfer Inefficiency: Non-condensable gases reduce the overall heat transfer capacity of the steam, making the system less efficient and potentially leading to suboptimal results in heating or sterilization processes.
-
- Corrosion: Gases like carbon dioxide can form corrosive compounds when dissolved in water or interact with metal surfaces, leading to long-term damage to steam system components.
Testing Non-Condensable Gases
Non-condensable gases are typically measured using gas analyzers that detect the presence and concentration of specific gases in the steam. Infrared sensors, paramagnetic analyzers, or thermal conductivity analyzers are commonly used to identify and quantify non-condensable gases. Maintaining low levels of these gases is essential for optimizing system performance and ensuring the purity of the steam.
4. Conductivity
Understanding the Role of Conductivity in Steam Quality
Conductivity testing is a method used to assess the level of dissolved solids or ionic impurities in steam. Conductivity is directly related to the presence of impurities such as salts, minerals, or other contaminants dissolved in the water before it is converted into steam. The key issues with high conductivity include:
-
- Scaling and Fouling: Dissolved solids can deposit onto the surfaces of heat exchangers, pipes, and boilers, leading to scaling. This buildup reduces the efficiency of heat transfer and can lead to corrosion over time.
-
- Impact on Sterilization: The presence of conductive contaminants can alter the heat transfer properties of steam, compromising the effectiveness of sterilization processes. For example, high conductivity can lower the steam temperature at which it operates, potentially leading to incomplete sterilization.
Testing Conductivity
Conductivity is measured using specialized conductivity meters that detect the electrical resistance of the steam. The higher the level of dissolved solids, the greater the conductivity. Steam used for pharmaceutical applications typically requires conductivity levels to be very low, often less than 1.3 µS/cm. Regular conductivity testing ensures that impurities are kept within acceptable limits and that the steam quality remains optimal.
5. Chemical Composition
The Importance of Chemical Composition in Pure Steam
The chemical composition of steam is crucial in assessing the overall purity of the steam and ensuring it is free from contaminants that could interfere with processes or affect product safety. Common chemical contaminants include:
-
- Chlorides and Sulfates: These ions can cause corrosion in steam systems and equipment, leading to the breakdown of components and contamination risks in sterile environments.
-
- Organic Compounds: Organic contaminants, often derived from the water source or the steam generation process, can negatively affect the safety and quality of products, particularly in pharmaceutical and food manufacturing.
-
- Heavy Metals: Trace amounts of metals like iron or copper can be introduced into steam from the piping or equipment. These impurities may cause chemical reactions that compromise the quality of the product being processed.
Testing Chemical Composition
Many industries depend on pure steam quality testing to ensure they meet regulatory standards and maintain safe practices. Understanding these standards is crucial for effective steam quality management.
The chemical composition of steam is analyzed using advanced techniques such as spectrometry, chromatography, or titration. These methods provide a detailed profile of the ionic and organic components in the steam. For high-purity applications, particularly in pharmaceuticals, ensuring the chemical composition of steam is free from contaminants is essential for regulatory compliance and product safety.
Methods of Pure Steam Quality Testing
Several methods are employed to test the quality of pure steam, depending on the specific parameters being analyzed. Some of the most common methods include:
1. Steam Sample Collection
Steam is typically sampled directly from the steam system and cooled to prevent further evaporation before testing. The sample is then tested for specific parameters like conductivity, moisture content, and chemical composition.
2. Conductivity Testing
Conductivity testing is one of the most common methods for measuring the purity of steam. This technique involves passing an electrical current through the steam sample and measuring its resistance. Higher conductivity levels indicate the presence of impurities in the steam, which can be harmful to both equipment and processes.
3. Moisture Testing
Moisture analyzers are used to detect the level of moisture present in steam. There are various techniques for moisture testing, such as gravimetric methods (weighing the steam sample before and after condensation) and infrared absorption methods, which provide real-time moisture content data.
4. Non-Condensable Gas Testing
To measure the presence of non-condensable gases in steam, gas analyzers are used. These devices can detect gases like oxygen, nitrogen, and carbon dioxide in the steam sample. The removal of these gases is crucial to maintain the purity of the steam.
5. Chemical Analysis
In some cases, a more detailed chemical analysis may be performed to identify trace elements or organic contaminants in the steam. Techniques such as chromatography or spectrometry are employed to provide in-depth insights into the chemical composition of the steam sample.
Read More: What You Need to Know About Industrial Gas Purity Testing: A Comprehensive Guide
Pure Steam Quality Testing Standards and Regulations
Pure steam plays a pivotal role in various industries, particularly in highly regulated sectors such as pharmaceuticals, biotechnology, and food processing. It is used extensively in sterilization, manufacturing, and laboratory processes where any deviation in steam quality could compromise product safety and efficacy. Therefore, it is essential that pure steam meets strict quality standards to ensure it remains free from contaminants and impurities, which could affect the integrity of the products being produced. Below are the key regulatory guidelines and standards governing pure steam quality across different industries.
1. USP <1231> Standard for Water for Injection (WFI)
Overview of USP <1231>
The United States Pharmacopeia (USP) is a recognized authority on pharmaceutical standards, and its USP <1231> standard provides comprehensive guidelines on the production of Water for Injection (WFI), including the role of pure steam in its sterilization processes. WFI is critical for pharmaceutical manufacturing, especially in the production of injectable drugs, as it must meet stringent purity requirements to ensure patient safety.
-
- Application of Pure Steam: In the production of WFI, pure steam is often used for sterilization because it provides a reliable means to eliminate microbial contamination. Steam is ideal for sterilizing large volumes of WFI since it is easily generated, distributes heat uniformly, and can be controlled to achieve the precise temperatures necessary for sterilization.
-
- Purity Requirements: Pure steam, in this case, must be free from any trace amounts of non-condensable gases, particulates, or chemicals. According to USP <1231>, steam must be “non-purified,” meaning that it cannot contain any chemical or physical contaminants that could potentially compromise the quality of WFI.
Key Elements of USP <1231>
-
- Bacterial Endotoxins: The presence of endotoxins in WFI could cause serious issues in injectable formulations, so steam sterilization must be effective in eliminating endotoxins from the water.
-
- Sterility Assurance: The standard provides guidelines for validating and monitoring the sterilization process, ensuring that pure steam meets the required sterility assurance levels (SAL) for pharmaceuticals.
2. EU GMP Guidelines
Overview of EU GMP Guidelines
The European Union’s Good Manufacturing Practice (GMP) guidelines are among the most stringent regulations for pharmaceutical manufacturing. These guidelines apply to all aspects of pharmaceutical production, including the use of pure steam. The EU GMP guidelines ensure that medicinal products are consistently produced and controlled to meet quality standards. Pure steam is integral to this process, particularly for sterilizing equipment, containers, and production lines.
-
- Steam Purity: Under EU GMP, steam used in pharmaceutical manufacturing must be free from contaminants such as particulates, non-condensable gases (e.g., air, carbon dioxide), and any residual chemicals. The steam should also be free from moisture, ensuring that it is in a dry, superheated state to meet the required sterilization parameters.
-
- Impact on Product Safety: The presence of contaminants in steam can lead to cross-contamination, which could compromise the safety and efficacy of the pharmaceutical products. EU GMP guidelines emphasize the need for consistent steam quality to prevent this risk.
Key Aspects of EU GMP Guidelines Regarding Pure Steam
-
- Sterilization and Cleaning: The guidelines outline specific requirements for the use of pure steam in cleaning and sterilization applications, ensuring that it reaches all areas of the equipment without introducing contaminants.
-
- Monitoring and Testing: Regular monitoring and testing of steam quality are mandatory to ensure compliance with EU GMP. Parameters such as temperature, pressure, moisture content, and non-condensable gases must be measured and controlled during the sterilization process.
-
- Validation: Pharmaceutical companies must validate their steam sterilization systems according to EU GMP, ensuring that pure steam meets the necessary requirements for effective sterilization.
3. FDA Regulations
Overview of FDA Regulations
The U.S. Food and Drug Administration (FDA) plays a critical role in regulating the use of pure steam in pharmaceutical manufacturing, particularly for sterilization purposes. The FDA enforces stringent guidelines to ensure that pharmaceutical products are manufactured safely and are free from contaminants, including those that may be introduced by steam systems.
-
- Compliance with CGMP: The FDA’s Current Good Manufacturing Practice (CGMP) regulations cover a wide range of aspects related to manufacturing processes, including the use of pure steam. Compliance with CGMP is mandatory for all pharmaceutical manufacturers in the U.S., and pure steam must meet specific quality standards to comply with these regulations.
-
- Ensuring Patient Safety: In accordance with FDA regulations, the use of pure steam in manufacturing must be controlled to eliminate any risk of contamination that could affect the safety, quality, or efficacy of the pharmaceutical products. This includes ensuring that steam systems are free from bacterial contamination, non-condensable gases, and other impurities that could affect product integrity.
Key FDA Guidelines for Pure Steam
-
- Microbial Control: Pure steam must be used in a way that ensures all microbial contamination is effectively eliminated during sterilization cycles. The FDA mandates the validation of steam sterilization processes to confirm that they achieve the required sterilization efficacy.
-
- Sterility Assurance Levels (SAL): The FDA requires that manufacturers demonstrate that their steam sterilization process consistently meets the appropriate SAL, ensuring a high level of confidence that all microorganisms are eliminated.
4. ASME Boiler and Pressure Vessel Code
Overview of ASME Boiler and Pressure Vessel Code
The American Society of Mechanical Engineers (ASME) Boiler and Pressure Vessel Code is a key standard that governs the design, construction, and operation of steam systems in industrial applications. This code ensures that steam systems operate safely, reliably, and in compliance with national safety standards.
-
- Steam System Design: The ASME Boiler and Pressure Vessel Code provides detailed guidelines on the safe design and operation of steam systems, which are crucial for generating pure steam. These guidelines ensure that steam is produced under optimal conditions, free from contaminants and capable of being used for a wide range of applications.
-
- Pressure and Temperature Control: According to ASME standards, steam systems must be designed to handle the pressures and temperatures required for specific applications. The code includes guidelines on pressure vessel safety, materials used in construction, and testing requirements to ensure the steam system is functioning efficiently.
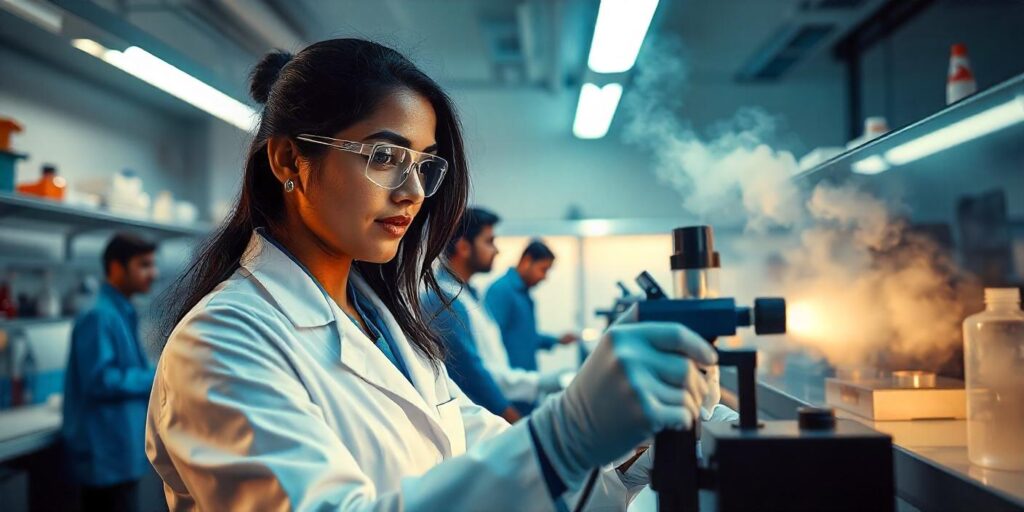
Key Elements of the ASME Code
Implementing best practices for pure steam quality testing can significantly enhance operational efficiency. Regular monitoring and testing are fundamental in achieving optimal steam purity.
-
- Pressure Vessel Safety: ASME sets strict requirements for pressure vessels used in steam systems to ensure they are built to withstand the high pressures associated with steam generation.
-
- Inspection and Maintenance: The ASME code outlines the procedures for inspecting and maintaining steam systems to ensure their continued safe operation. Regular maintenance ensures that the steam produced is free from impurities and contaminants.
-
- Testing: ASME guidelines require that steam systems be regularly tested to ensure that pure steam is produced under the right conditions. These tests cover aspects such as pressure, temperature, and steam purity.
Read More: Real-World Applications of Disinfectant Efficacy Testing in Pharma and Biotech
Best Practices for Maintaining Pure Steam Quality
At Prewel labs, we provide expert solutions for pure steam quality testing, ensuring compliance with industry regulations and maintaining the highest purity levels in steam systems.
Our team is dedicated to assisting clients with pure steam quality testing, delivering tailored services to meet the diverse needs of various industries.
Ensuring consistent steam quality requires proactive monitoring and regular maintenance of steam systems. Here are some best practices to maintain the quality of pure steam:
-
- Regular Testing: Conduct regular purity testing using the appropriate methods for conductivity, moisture content, and non-condensable gases to ensure that steam meets quality standards.
-
- Proper Maintenance: Regularly inspect and maintain steam generators, boilers, and associated piping systems to minimize the risk of contamination and corrosion.
-
- Optimize Steam Generation Conditions: Ensure that steam is produced at the correct temperature and pressure to prevent the formation of non-condensable gases or moisture.
-
- Filtration and Purification: Implement filtration systems to remove impurities from water before it is vaporized, ensuring the resulting steam is free from contaminants.
-
- System Validation: Periodically validate steam sterilization systems to confirm that they meet regulatory standards and operate efficiently.
How Prewellabs Can Help with Pure Steam Quality Testing
At Prewel labs, we understand the critical role that pure steam plays in industries like pharmaceuticals, biotechnology, and food processing. Ensuring that your steam meets regulatory standards and maintains the highest level of purity is essential for the safety and efficacy of your products. We offer comprehensive pure steam quality testing and consulting services tailored to meet the unique requirements of your steam systems.
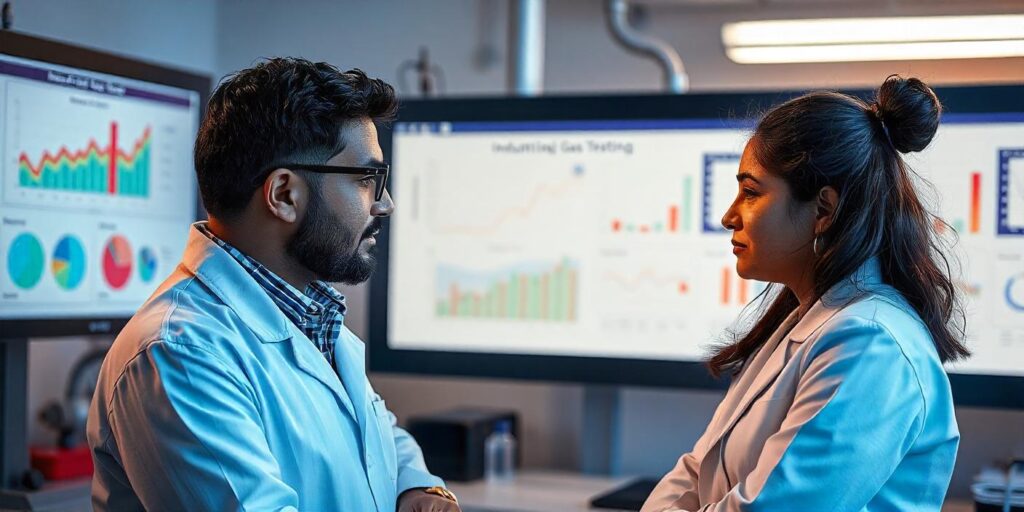
FAQs
1. What is pure steam, and why is it important?
Pure steam is steam that is free from impurities such as moisture, non-condensable gases, and dissolved solids. It is crucial in industries like pharmaceuticals, biotechnology, and food processing, where it is used for sterilization and other critical applications. Ensuring pure steam quality is vital for product safety, equipment longevity, and regulatory compliance.
2. What parameters are tested to determine pure steam quality?
The key parameters tested in pure steam quality include temperature, pressure, moisture content, non-condensable gases, conductivity, and chemical composition. These factors ensure that the steam meets the necessary standards for purity and efficiency in various industrial processes.
3. How can moisture in steam affect industrial processes?
Excess moisture in steam can lead to equipment corrosion, reduced sterilization efficiency, and inconsistent system performance. Moisture can also damage sensitive equipment like turbines, leading to costly repairs and unplanned downtime.
4. How do non-condensable gases affect pure steam systems?
Non-condensable gases such as air and carbon dioxide can interfere with the sterilization process, reduce steam system efficiency, and potentially contaminate products. These gases must be removed to ensure optimal steam quality and maintain system performance.
5. What are the regulatory standards for pure steam quality?
Regulatory standards for pure steam quality include the USP <1231> for Water for Injection (WFI), EU GMP guidelines for pharmaceutical manufacturing, FDA regulations for steam used in drug production, and ASME Boiler and Pressure Vessel Code for steam system design and safety. These guidelines ensure steam quality is maintained to protect product safety and meet legal requirements.
6. How can I ensure my steam system complies with regulatory standards?
To ensure compliance with regulatory standards, it is essential to regularly test steam quality, maintain proper documentation, and validate your sterilization processes. Working with an experienced testing and consulting partner, like Prewellabs, can help ensure ongoing compliance with the latest industry regulations.
7. What are the methods in pure steam quality testing?
Common testing methods for analyzing pure steam quality include conductivity testing, moisture content analysis, gas chromatography, and mass spectrometry. These tests help measure the concentration of impurities and ensure that the steam meets the required quality standards.
8. Why is conductivity testing important in pure steam quality analysis?
Conductivity testing is used to measure the level of dissolved solids in steam. Higher conductivity levels indicate the presence of impurities, which can affect steam quality, system efficiency, and the overall sterilization process. Ensuring low conductivity is essential for maintaining pure steam.
By prioritizing pure steam quality testing, industries can enhance product safety and efficacy, reinforcing their commitment to quality and compliance.
9. What is the role of pure steam in sterilization processes?
Pure steam is used in sterilization because it is effective at killing bacteria, viruses, and other microorganisms. It is an essential component in industries like pharmaceuticals and healthcare, where sterility is critical for product safety and patient health.
10. How can Prewellabs assist in pure steam quality testing?
Prewellabs provides comprehensive testing services for pure steam quality, including monitoring key parameters such as moisture content, pressure, temperature, and non-condensable gases. We also offer consulting, system audits, validation, and regulatory compliance services, helping clients maintain high-quality steam systems that meet industry standards.
Conclusion
Pure steam is a critical component in many industrial processes, particularly in sectors that demand high levels of cleanliness and precision. Regular testing and monitoring of steam quality are essential for maintaining operational efficiency, ensuring regulatory compliance, and safeguarding product quality. By understanding the key parameters, testing methods, and best practices for pure steam quality, industries can optimize their steam systems, reduce operational risks, and ensure that their products meet the highest standards of purity and safety.
Authors
-
Surendra is an Assistant Manager in the Utility Testing Department with over 8 years of experience in steam, compressed air, and industrial gas purity testing. He has worked with leading testing service providers, including SGS, and has conducted on-site testing for top manufacturing, pharmaceutical, and food & beverage industries such as Merck, Biocon, Coca-Cola, and many others. Passionate about quality and compliance, he shares technical insights to help industries maintain optimal utility standards.
View all posts -
Arjun Jha has over 8 years of experience in tech startups, business strategy, and digital and traditional marketing. He’s helped many startups grow by using creative strategies and a deep understanding of the market. Outside of work, Arjun enjoys reading about business, philosophy, psychology, and spirituality, which inspires his unique approach to problem-solving and growth.
View all posts -
With an abundance of experience in the field of SEO, Adithya is someone who is curious about the domain. He has published over 700 articles under his name and has worked for companies like EssentiallySports, TCS, and more.
View all posts