Compressed air is a vital resource in many industries, powering equipment, tools, and systems essential to operations. However, to ensure the safety, efficiency, and reliability of systems that rely on compressed air, it is critical to perform regular compressed air testing. This pillar blog explores the significance of compressed air testing, the key parameters involved, testing methods, challenges, and how businesses can benefit from comprehensive air quality monitoring.
What is Compressed Air Testing?
Compressed air testing is a critical process used to assess the quality and purity of compressed air systems used across industries. Compressed air, often considered the “fourth utility” after electricity, water, and gas, is essential for powering machinery, tools, and various processes in manufacturing, pharmaceuticals, food processing, and other sectors. Given its pervasive role, ensuring the quality of compressed air is vital for maintaining safety, operational efficiency, and product quality. This testing involves a systematic evaluation of air purity, contamination levels, and system efficiency to ensure that the compressed air used in production systems is free from harmful particles, moisture, oil, or microbial contaminants.
Compressed air systems typically comprise several components, such as compressors, air dryers, filtration systems, and distribution pipes. However, despite being an essential utility, compressed air systems can easily become contaminated, affecting product quality and system performance. The primary goal of compressed air testing is to detect such contaminants and verify that the air is safe for use in critical processes.
Why is Compressed Air Testing Essential?
Compressed air, when contaminated, can pose significant risks to both the products being manufactured and the equipment within a production facility. In some industries, such as food and beverage, pharmaceuticals, and medical device manufacturing, compressed air is used directly in the product itself or comes into contact with products during the manufacturing process. Contaminants like moisture, oil, and microbial growth can lead to costly product defects, health and safety hazards, equipment damage, and regulatory non-compliance.
Key Objectives of Compressed Air Testing
- Assessing Air Purity: The primary aim of compressed air testing is to assess the purity of the air being used in the production processes. For specific applications, especially in sensitive industries such as pharmaceuticals, food processing, and electronics manufacturing, the air needs to be free from contaminants like moisture, particulates, oil, or bacteria. Testing helps ensure the air is clean and safe for use in these critical operations, and it is consistent with the required purity standards for the intended application.
- Ensuring Compliance with Regulatory Standards: Different industries are governed by stringent air quality standards, and compressed air must meet these standards to avoid penalties or violations. For instance, in pharmaceutical manufacturing, compressed air must meet the standards set by the U.S. Food and Drug Administration (FDA) and the European Medicines Agency (EMA). Similarly, in food production, the compressed air used must comply with good manufacturing practices (GMP). Testing ensures that the compressed air meets these regulatory standards and avoids costly non-compliance issues.
- Preventing Contamination: Contaminants in compressed air systems can compromise both the quality of the product being manufactured and the efficiency of the machines using the air. For instance, moisture in the air can cause rust, corrosion, and clogging in pipes and equipment, while oil and particulate matter can affect the quality of products, especially those that require high cleanliness, such as food and drugs. Regular testing helps identify any contamination early, enabling preventive measures to be taken before problems arise.
- Improving System Efficiency: A well-maintained compressed air system can significantly reduce energy consumption and maintenance costs, while boosting production efficiency. Regular testing can identify issues such as leaks, improper filtration, or inefficiencies in air compressors and dryers. By detecting and rectifying these issues, businesses can ensure that their compressed air systems operate at peak performance, reducing the risk of downtime and avoiding excessive energy usage.
Why is Compressed Air Testing Important?
Compressed air is often called the “fourth utility” in manufacturing due to its widespread use in powering machines, tools, and processes. However, if the quality of compressed air deteriorates, it can have serious consequences. Here are some key reasons why compressed air testing is essential:
Read More:Master the A-Z of Disinfectant Efficacy Testing: Now Achieve Clean Pharmaceutical Environments
- Health and Safety: Contaminated compressed air can lead to the inhalation of harmful substances, potentially endangering worker health. For example, oil vapors or bacterial contamination can pose health risks in sectors like food processing and pharmaceuticals.
- Product Quality: In many industries, such as pharmaceuticals, food production, and electronics, compressed air is used in direct contact with products. Any contamination in the air supply could result in defects, product spoilage, or even recalls.
- Equipment Longevity: Contaminants like moisture and oil can cause corrosion, clog filters, and lead to premature wear of equipment and machinery. Regular testing ensures that the system is clean and running efficiently, extending the life of the compressed air equipment.
- Regulatory Compliance: Many industries have stringent guidelines on air quality. For instance, the FDA requires high levels of cleanliness for compressed air in pharmaceutical and food manufacturing. Testing helps companies stay compliant with these regulations.
Key Parameters in Compressed Air Testing
Compressed air is an essential utility in numerous industrial processes, ranging from powering machinery to ensuring the quality of finished products. The purity of compressed air is critical to ensuring the reliability of operations, preventing equipment damage, maintaining product quality, and adhering to regulatory standards. Key parameters are tested to evaluate compressed air quality, which can vary depending on the industry and the specific application. Regular testing of these parameters helps maintain the efficiency, safety, and compliance of compressed air systems.
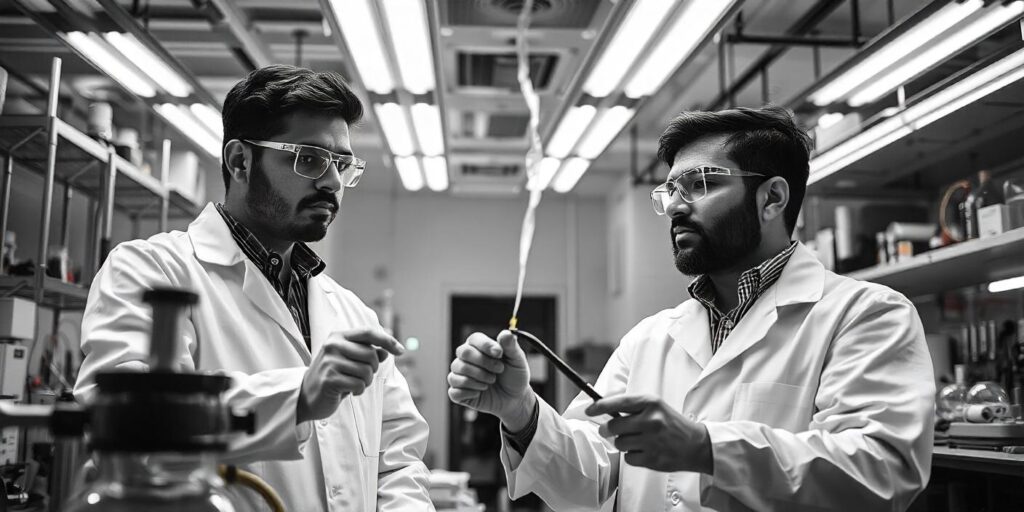
Here are the key parameters in compressed air testing:
1. Oil Content
Oil contamination is one of the most common and problematic issues in compressed air systems. Oil can enter the system through compressor lubrication or as a byproduct of the compression process. This can have several adverse effects on the compressed air quality and the equipment that uses it. The presence of oil in compressed air can cause:
-
- Damage to Sensitive Equipment: Oil can clog filters, reduce the efficiency of pneumatic tools, and cause wear on machinery and components. It may also damage delicate instruments used in industries like food processing and pharmaceuticals.
-
- Product Contamination: Oil can transfer to the end products, compromising their purity and safety, especially in critical sectors like food and drug manufacturing. Contaminated products can result in costly recalls, fines, and a damaged reputation.
-
- Health Risks: In industries where compressed air comes into direct contact with consumables or pharmaceuticals, oil contamination can pose serious health risks to consumers.
Oil content in compressed air systems is tested using specialized instruments such as oil sensors or by collecting samples for laboratory analysis. Testing ensures that the oil levels are within safe, allowable limits set by regulatory standards.
2. Moisture Content
Moisture in compressed air is one of the most prevalent contaminants that can cause a range of operational issues. If not properly removed, moisture can result in:
-
- Corrosion and Rust: Excess moisture in compressed air systems can lead to rusting and corrosion of pipelines, equipment, and components, which can cause long-term damage and increased maintenance costs.
-
- Bacterial Growth: Moisture provides a conducive environment for microbial growth, which is particularly concerning in industries such as pharmaceuticals and food manufacturing, where cleanliness and hygiene are paramount.
-
- Freezing in Winter: In colder climates, moisture in compressed air can freeze, obstructing air flow and causing damage to valves, pipes, and other components, leading to system failure.
-
- Contamination of Products: In certain applications, such as food or drug production, moisture can mix with the product, leading to spoilage or degradation.
Testing for moisture typically involves measuring the dew point, which indicates the temperature at which water vapor in the air will begin to condense. Regular moisture testing ensures that air dryers are operating correctly, and that the moisture content is controlled to maintain product and equipment integrity.
3. Particulate Matter
Particulate contamination in compressed air refers to any solid particles—such as dust, dirt, or rust—that are carried through the system. These particles can cause significant issues in industries where air purity is critical. Potential problems include:
-
- Damage to Equipment: Particulates can wear down pneumatic components, clog filters, and interfere with the functioning of machinery.
-
- Contamination of Products: Dust or dirt carried by compressed air can taint products, particularly in the pharmaceutical, food, and electronics industries, where even minute particles can affect product quality.
-
- Decreased Air Quality: Particles can reduce the effectiveness of the compressed air, leading to decreased efficiency in manufacturing processes.
To test for particulate contamination, particle counters are used to detect the number, size, and type of particles in the compressed air. Depending on the industry, specific particulate size limits may be imposed, particularly in highly regulated environments such as medical device manufacturing or semiconductor production.
4. Microbial Contamination
Microbial contamination, including bacteria, fungi, and viruses, is a major concern, especially in industries like pharmaceuticals, healthcare, food and beverage, and medical device manufacturing. Microbial contaminants can lead to a range of issues:
-
- Health and Safety Risks: Bacteria or fungi in the air can contaminate products or create hazardous environments for workers.
-
- Product Contamination: Microbial growth in compressed air systems can spread to products, particularly in the pharmaceutical and food industries, leading to potential health risks and quality issues.
-
- Regulatory Violations: Non-compliance with hygiene standards due to microbial contamination can lead to costly fines, recalls, and loss of business.
Microbial testing typically involves monitoring air samples for bioburden or measuring the presence of specific microorganisms. Methods include culture-based tests, where samples are taken and incubated, as well as real-time detection systems that identify microbial content instantly.
5. Carbon Monoxide (CO)
Carbon monoxide (CO) is a dangerous, odorless, and colorless gas that can pose serious health risks, particularly in environments where compressed air is used in high volumes. This contaminant is most common in systems powered by internal combustion engines, such as those found in some industrial applications. The presence of CO can cause:
-
- Health Hazards: CO poisoning can occur when the air is used in confined spaces, putting workers at risk.
-
- Damage to Products: In industries like pharmaceuticals and food production, CO contamination could jeopardize product safety, especially if the compressed air is in direct contact with the products.
-
- Regulatory Non-compliance: Exposure to CO is heavily regulated, and failure to monitor or control its levels could lead to penalties.
CO levels are typically measured using specialized gas detectors or sensors. Regular testing ensures the air is free from this hazardous gas and adheres to safety regulations.
Read More: What You Need to Know About Industrial Gas Purity Testing: A Comprehensive Guide
6. Hygiene and Bioburden Testing
Bioburden testing evaluates the microbial load within compressed air, particularly in sensitive industries like pharmaceuticals, healthcare, and medical device manufacturing. This testing is essential for ensuring the air meets stringent hygiene standards. The presence of microorganisms in the air can:
-
- Compromise Product Quality: In industries where air directly contacts products (such as injectable drugs, surgical instruments, or food), bioburden can significantly affect product quality.
-
- Pose Risks to Human Health: Contaminated air can lead to infections or other health hazards, especially in hospitals, laboratories, and food facilities.
Bioburden testing involves collecting air samples and analyzing them for microbial contamination, including bacteria, molds, and yeasts. Specific standards or limits are often set by industry regulations to ensure compressed air quality and prevent any microbial contamination from affecting the end products.
Methods of Compressed Air Testing
There are various methods to test the quality of compressed air, each suited for different contaminants and testing requirements. Here are some of the most common testing methods:
-
- Grab Sampling:
-
- Grab sampling involves collecting a single sample of compressed air at a specific moment in time to evaluate parameters like oil content, moisture levels, and particulate matter. This method provides a snapshot of air quality, but may not account for variations over time.
-
- Grab Sampling:
-
- Continuous Monitoring:
-
- Continuous monitoring uses sensors to track air quality in real time. This method is ideal for detecting fluctuations in moisture, oil, or contaminants that may impact system performance or product quality. Continuous data collection also helps ensure compliance with regulatory limits.
-
- Continuous Monitoring:
-
- Laboratory Analysis:
-
- Samples of compressed air can be taken and sent to a laboratory for detailed analysis. Laboratory testing provides in-depth information about the composition of the air, including the presence of specific contaminants like oil, microbes, and gases.
-
- Laboratory Analysis:
-
- Particle Counters:
-
- Specialized instruments such as particle counters can be used to measure the size and quantity of particles in the compressed air. This is particularly useful for industries like electronics or pharmaceuticals, where even minute particulate contamination can affect production.
-
- Particle Counters:
-
- Dew Point Testing:
-
- Dew point testing measures the temperature at which moisture in the compressed air will condense into water. By monitoring the dew point, businesses can ensure that moisture is effectively removed from the air system.
-
- Dew Point Testing:
Read More: Seal Strength Testing: Importance, Standards, Protocols, and Advanced Considerations
Challenges in Compressed Air Testing
While compressed air testing is essential for ensuring air quality, it does come with its challenges:
-
- Complexity of Air Systems:
-
- Compressed air systems can be complex, with multiple components like filters, dryers, and regulators that influence air quality. Testing the entire system requires careful planning and thorough testing of each component.
-
- Complexity of Air Systems:
-
- Cost of Testing:
-
- Regular compressed air testing can incur costs, especially when continuous monitoring systems or laboratory analysis are required. However, this cost is outweighed by the potential savings from preventing downtime, equipment failure, and product defects.
-
- Cost of Testing:
-
- Regulatory Compliance:
-
- Industries like pharmaceuticals, food, and medical device manufacturing must adhere to strict regulatory requirements for compressed air quality. Staying compliant requires ongoing testing, which can be resource-intensive.
-
- Regulatory Compliance:
-
- Interpreting Test Results:
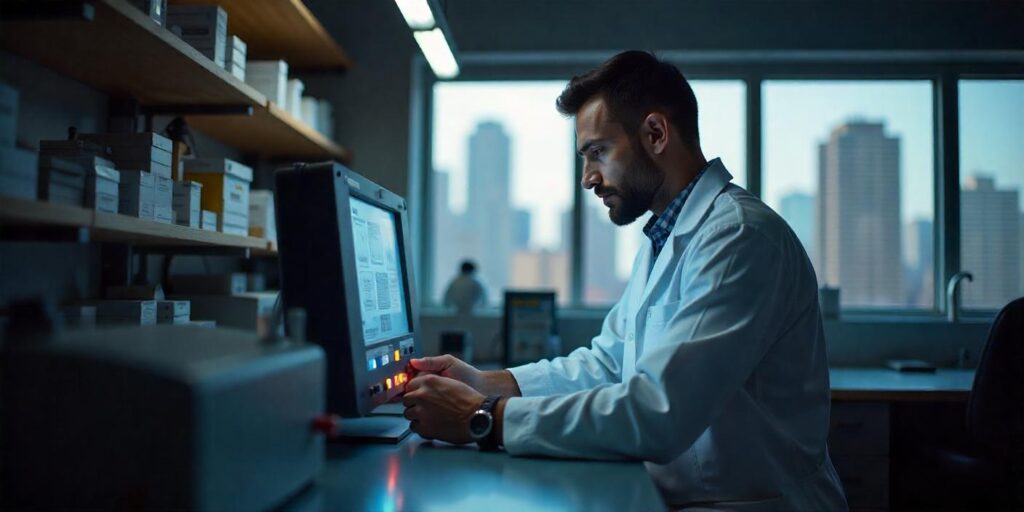
-
- Understanding and interpreting test results correctly is crucial for identifying issues and taking corrective actions. Incorrect interpretation can lead to overlooking critical contaminants or underestimating potential risks.
Frequently asked questions (FAQs) related to compressed air testing:
-
- What is compressed air testing? Compressed air testing is the process of evaluating the quality and purity of compressed air systems used in industrial and manufacturing processes. It involves checking for contaminants such as oil, moisture, particulates, and microbial contamination to ensure compliance with regulatory standards and operational efficiency.
-
- Why is compressed air testing important? Compressed air testing is crucial to ensure that the air used in manufacturing or production processes is free from harmful contaminants that could damage equipment, compromise product quality, or pose health risks, particularly in industries like pharmaceuticals, food and beverage, and healthcare.
-
- How often should compressed air testing be performed? The frequency of compressed air testing depends on the specific industry and its regulatory requirements. In highly regulated sectors like pharmaceuticals, testing may be required more frequently (e.g., quarterly), while in other industries, it may be performed annually or during scheduled maintenance.
-
- What contaminants are typically tested for in compressed air? Common contaminants tested in compressed air include oil, moisture, particulate matter, carbon monoxide (CO), and microbial contamination (bacteria, mold, fungi). The levels of these contaminants are evaluated to ensure the air quality meets operational standards and industry regulations.
-
- What is the role of moisture testing in compressed air systems? Moisture in compressed air can cause corrosion, rust, and the growth of bacteria. Moisture testing ensures that the compressed air system has adequate drying mechanisms in place, preventing water vapor from affecting equipment performance or product quality.
-
- What are the risks of oil contamination in compressed air? Oil contamination can cause damage to pneumatic equipment, clog filters, reduce efficiency, and compromise product quality, particularly in industries where compressed air directly contacts food or pharmaceuticals. Testing ensures that oil content is kept within permissible limits.
-
- How is microbial contamination in compressed air tested? Microbial contamination is tested by collecting air samples and analyzing them for bacteria, molds, or fungi. Testing is critical in industries such as pharmaceuticals and healthcare, where air hygiene is directly linked to product safety and compliance with health regulations.
-
- What equipment is used for compressed air testing? Various instruments are used for compressed air testing, including particle counters for particulate matter, moisture analyzers for dew point measurements, oil sensors for detecting oil levels, and gas detectors for substances like carbon monoxide. These devices help monitor and maintain air quality.
-
- What is bioburden testing in compressed air? Bioburden testing evaluates the microbial load in compressed air, particularly in sensitive industries like medical devices and pharmaceuticals. It ensures the air meets strict hygiene standards and does not contaminate products or compromise safety.
-
- What are the regulatory standards for compressed air testing? Regulatory standards for compressed air testing vary by industry and region. For example, in pharmaceuticals, guidelines from the FDA, ISO, and GMP require compressed air systems to meet specific purity levels. Other industries may follow standards set by organizations like OSHA or local environmental agencies to ensure safe and compliant operations.
How Prewel Labs Can Help with Compressed Air Testing
Prewel Labs offers comprehensive compressed air testing solutions designed to meet the needs of various industries. Our services include:
-
- Regulatory Compliance Support:
-
- We ensure your compressed air systems meet industry-specific regulations, such as FDA, ISO, and GMP guidelines, providing documentation and recommendations for compliance.
-
- Regulatory Compliance Support:
-
- Custom Testing Solutions:
-
- We offer tailored testing services to address the unique needs of your compressed air system, including oil content, moisture levels, microbial contamination, and particulate matter.
-
- Custom Testing Solutions:
-
- Continuous Monitoring:
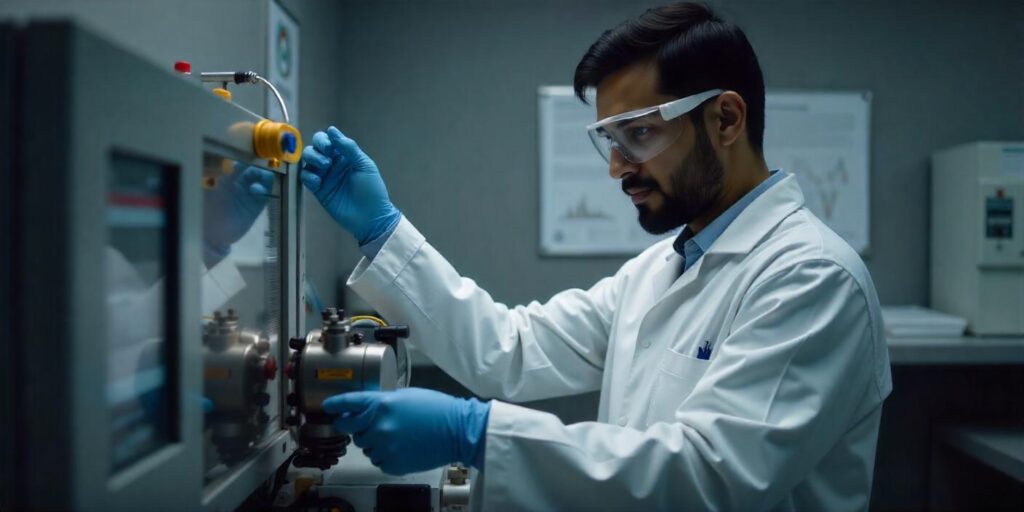
-
- Our advanced continuous monitoring solutions provide real-time data on the quality of your compressed air, allowing you to identify issues before they cause significant problems.
-
- Consultation and Optimization:
-
- Beyond testing, we provide consultation services to help optimize your compressed air systems, improving efficiency and reducing operational costs.
-
- Consultation and Optimization:
Conclusion
Compressed air is a critical component in many industrial and manufacturing processes, and its quality directly impacts equipment performance, product safety, and operational efficiency. Regular compressed air testing ensures that systems are free from harmful contaminants, such as moisture, oil, particulate matter, and microbes, which could otherwise lead to equipment malfunctions, safety risks, or compromised product quality. By adhering to rigorous testing protocols and complying with industry regulations, businesses can optimize their compressed air systems, reduce downtime, and maintain a safe, efficient, and compliant production environment.
Investing in comprehensive compressed air testing not only protects equipment and product quality but also ensures long-term operational success. Whether you’re in pharmaceuticals, food and beverage, or any other critical sector, maintaining air purity is essential for safeguarding both the bottom line and public health. By partnering with experts in compressed air testing, companies can stay ahead of potential issues, optimize system performance, and remain compliant with regulatory requirements.
Authors
-
Surendra is an Assistant Manager in the Utility Testing Department with over 8 years of experience in steam, compressed air, and industrial gas purity testing. He has worked with leading testing service providers, including SGS, and has conducted on-site testing for top manufacturing, pharmaceutical, and food & beverage industries such as Merck, Biocon, Coca-Cola, and many others. Passionate about quality and compliance, he shares technical insights to help industries maintain optimal utility standards.
View all posts -
With an abundance of experience in the field of SEO, Adithya is someone who is curious about the domain. He has published over 700 articles under his name and has worked for companies like EssentiallySports, TCS, and more.
View all posts -
Arjun Jha has over 8 years of experience in tech startups, business strategy, and digital and traditional marketing. He’s helped many startups grow by using creative strategies and a deep understanding of the market. Outside of work, Arjun enjoys reading about business, philosophy, psychology, and spirituality, which inspires his unique approach to problem-solving and growth.
View all posts