Compressed air systems are integral to numerous industries, particularly in sectors such as pharmaceuticals, food processing, and electronics manufacturing. Ensuring the air quality within these systems meets stringent standards is crucial, especially for compressed air testing, but achieving this can be fraught with challenges. Below, we explore the 10 key challenges in compressed air testing and provide actionable strategies to overcome them.
1. Identifying Contaminants
Compressed air can harbor various contaminants, including oil vapor, particulate matter, and microorganisms. Accurately identifying these contaminants is essential but often complex due to the diversity of potential impurities and their sources.
Understanding the importance of compressed air testing is essential for maintaining high-quality standards in your operations.
- Challenge Details: Contaminants can originate from various points in the compressed air system, including compressors, filters, or even environmental air intake. Some contaminants, like oil vapor, require specialized detection methods.
- Solution: Employ advanced analytical tools like gas chromatography for oil vapor and laser particle counters for particulate matter. For microbiological testing, use agar-based impaction or rapid molecular methods. Routine testing schedules should be established to ensure continuous monitoring.
2. Maintaining Sampling Integrity
In the realm of compressed air testing, it is vital to maintain sampling integrity to ensure accurate results.
Improper sampling techniques or equipment can compromise the integrity of the collected sample, leading to inaccurate results and misinformed decisions.
- Challenge Details: Sampling errors often arise from inadequate equipment sterilization, poor handling practices, or sampling from unrepresentative points in the system.
- Solution: Use ISO-certified sampling devices designed to prevent contamination. Train personnel on proper sampling procedures and establish protocols that ensure consistency.
Regulatory compliance in compressed air testing can be complicated, but staying informed about standards is key to success.
Read More: What You Need to Know About Compressed Air Testing: A Comprehensive Guide
3. Meeting Regulatory Standards
Standards like ISO 8573-1 and GMP guidelines define specific limits for contaminants, which can be challenging to meet consistently due to variations in system performance and environmental factors.
Regular equipment calibration is crucial in the realm of compressed air testing, ensuring accuracy and reliability.
- Challenge Details: Regulatory requirements are complex and differ across industries and regions. Non-compliance can lead to penalties, production delays, and compromised product safety.
- Solution: Partner with accredited testing laboratories that specialize in regulatory compliance. Regularly update testing protocols to reflect changes in standards, and implement corrective actions when deviations occur.
4. Equipment Calibration
Environmental influences can significantly impact compressed air testing results, necessitating controlled conditions.

Uncalibrated testing equipment can yield inaccurate results, leading to potential non-compliance and operational risks.
- Challenge Details: Calibration errors can occur over time due to wear and tear, exposure to extreme conditions, or lack of routine maintenance.
- Solution: Establish a routine calibration schedule using certified reference materials. Maintain detailed calibration logs to ensure traceability and accountability.
Training personnel in proper compressed air testing protocols is essential for maintaining quality standards.
5. Environmental Influences
Factors like temperature, humidity, and environmental contaminants can affect compressed air quality and skew test results.
Selecting appropriate sampling points is crucial in compressed air testing to ensure representative results.
- Challenge Details: Uncontrolled environmental conditions can introduce moisture, particulate matter, or biological contaminants into the compressed air system.
- Solution: Conduct testing under controlled environmental conditions. Utilize air dryers or desiccant systems to manage moisture, and install filters to minimize particulate intrusion.
6. Training Personnel
Microbial contamination detection is a significant aspect of compressed air testing, requiring proactive measures.
A lack of training in testing procedures and equipment handling often leads to errors and inconsistencies.
- Challenge Details: Untrained personnel may mishandle testing equipment, misinterpret results, or overlook critical parameters.
- Solution: Invest in regular training programs for all personnel involved in compressed air testing. Offer certification opportunities and hands-on practice to enhance skill levels.
Cost management strategies are vital in ensuring that compressed air testing remains economically viable.
7. Selecting Sampling Points
Inappropriate selection of sampling points may not provide a representative assessment of the entire system’s air quality.
Regular maintenance of your compressed air system is essential for effective compressed air testing and compliance.
- Challenge Details: Sampling from random or convenient locations can misrepresent the system’s overall air quality, leading to flawed conclusions.
- Solution: Develop a comprehensive system diagram and strategically select sampling points near critical usage areas. Validate the sampling plan periodically to ensure it reflects current operational conditions.
8. Microbial Contamination Detection
By partnering with us, you gain access to expert knowledge in compressed air testing, enhancing your operational efficiency.
Microbial contamination can grow over time, complicating its detection and control.
- Challenge Details: Microbes can colonize air distribution lines, filters, and storage tanks, posing risks to sensitive products.
- Solution: Use rapid microbiological methods, such as ATP bioluminescence, for quick detection and validation. Conduct regular sterilization and cleaning of system components to prevent microbial growth.
9. Cost Management
Frequent testing, though necessary, can strain operational budgets and lead to resource allocation challenges.
- Challenge Details: Balancing cost efficiency with regulatory and operational requirements can be difficult, especially for smaller facilities.
- Solution: Implement a risk-based testing schedule that prioritizes high-risk areas while maintaining periodic testing across the system. Leverage bulk testing packages from certified labs to reduce costs.
Read More: What You Need to Know About Industrial Gas Purity Testing: A Comprehensive Guide
10. System Maintenance Issues
Poorly maintained compressed air systems can introduce contaminants, complicating testing and compliance efforts.
- Challenge Details: Maintenance issues, such as clogged filters, leaks, or oil carryover, often go unnoticed until they cause significant contamination.
- Solution: Develop a robust preventive maintenance program that includes regular inspections, filter replacements, and leak checks. Use predictive maintenance tools to address potential issues proactively.
How Prewel Labs Can Help
At Prewel Labs, we understand the complexities of compressed air testing and the challenges you face. Here’s how we can support you:
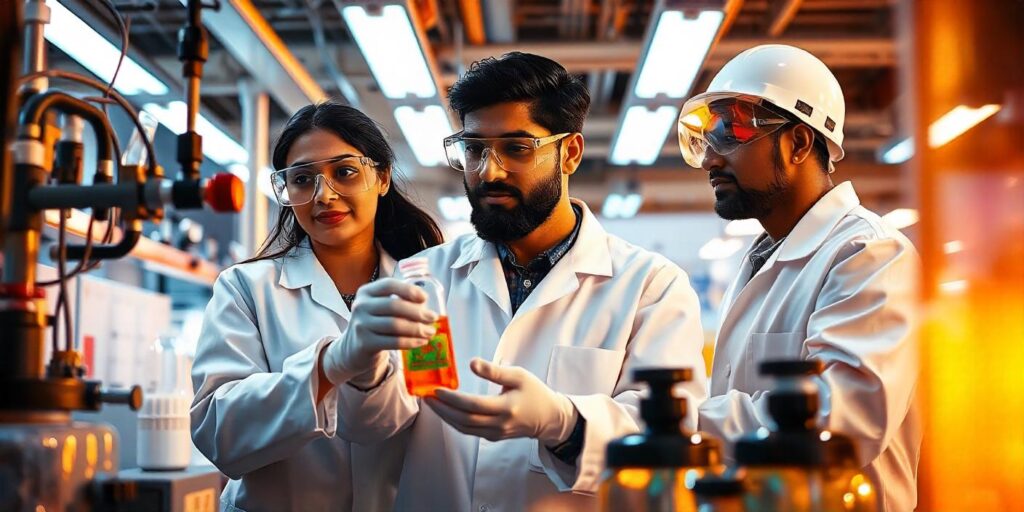
- Comprehensive Testing Services: We offer a wide range of tests for particulate matter, oil vapor, moisture, and microbial contamination, ensuring compliance with ISO 8573-1 and GMP standards.
- Advanced Equipment and Techniques: Our state-of-the-art facilities and certified experts ensure accurate and reliable results every time.
- Customized Solutions: We tailor our testing protocols to your specific industry needs and operational requirements, providing actionable insights for improvement.
- Regulatory Compliance Support: Our team stays updated with the latest regulatory changes and helps you maintain compliance effortlessly.
- Training and Consultation: We provide training sessions for your personnel and consultative support to optimize your compressed air system.
With Prewel Labs as your partner, you can overcome these challenges and ensure the quality and safety of your compressed air systems.
Conclusion
Compressed air testing is a critical aspect of quality assurance in many industries. While challenges abound, adopting a proactive approach, leveraging advanced technologies, and partnering with experts like Prewel Labs can ensure compliance and reliable air quality. By addressing these 10 challenges with targeted strategies, businesses can maintain optimal system performance and regulatory compliance.
Authors
-
Surendra is an Assistant Manager in the Utility Testing Department with over 8 years of experience in steam, compressed air, and industrial gas purity testing. He has worked with leading testing service providers, including SGS, and has conducted on-site testing for top manufacturing, pharmaceutical, and food & beverage industries such as Merck, Biocon, Coca-Cola, and many others. Passionate about quality and compliance, he shares technical insights to help industries maintain optimal utility standards.
View all posts -
With an abundance of experience in the field of SEO, Adithya is someone who is curious about the domain. He has published over 700 articles under his name and has worked for companies like EssentiallySports, TCS, and more.
View all posts -
Arjun Jha has over 8 years of experience in tech startups, business strategy, and digital and traditional marketing. He’s helped many startups grow by using creative strategies and a deep understanding of the market. Outside of work, Arjun enjoys reading about business, philosophy, psychology, and spirituality, which inspires his unique approach to problem-solving and growth.
View all posts