In industries where precision, safety, and quality are paramount, the purity of industrial gases plays a critical role. From ensuring the integrity of pharmaceutical products to maintaining optimal performance in manufacturing, industrial gas purity testing is indispensable. This comprehensive guide explores the importance, methods, and best practices for industrial gas purity testing, providing you with the insights needed to safeguard your operations.
What Is Industrial Gas Purity Testing?
Industrial gas purity testing is the process of analyzing gases used in various industries to ensure they meet specific quality and purity standards. Commonly tested gases include oxygen, nitrogen, argon, hydrogen, helium, and carbon dioxide. These gases are integral to numerous industrial applications, making their purity critical for operational success.
Key Applications of Industrial Gases:
- Pharmaceuticals: Used as excipients or during drug manufacturing processes to maintain product stability and efficacy. Impurities in gases like oxygen or nitrogen can affect the chemical composition and therapeutic properties of pharmaceuticals.
- Food and Beverage: Essential for packaging, carbonation, and preservation. For example, carbon dioxide is used to carbonate drinks, while nitrogen helps in food packaging to extend shelf life by displacing oxygen.
- Healthcare: Critical in medical devices, surgical procedures, and as respiratory gases. The purity of oxygen and other medical gases directly impacts patient safety and treatment outcomes.
- Electronics: Necessary for semiconductor manufacturing and other precision applications. Impurities in gases like argon or nitrogen can compromise the integrity of microelectronic components.
- Energy: Fundamental for hydrogen fuel cells and other energy-related technologies. Purity in gases like hydrogen ensures the efficiency and longevity of energy systems.
Read More: What You Need to Know About Compressed Air Testing: A Comprehensive Guide
Purpose of Industrial Gas Purity Testing:
By assessing gas composition, contaminants, and trace elements, industrial gas purity testing:
- Ensures Compliance: Aligns with regulatory standards set by organizations like ISO, USP, and GMP, ensuring safe and legal operations.
- Protects Equipment: Prevents damage or wear caused by impurities such as moisture or particulates.
- Enhances Safety: Reduces risks associated with hazardous contaminants that could endanger workers or compromise product safety.
- Improves Efficiency: Supports optimal performance in processes like welding, laser cutting, or chemical reactions.
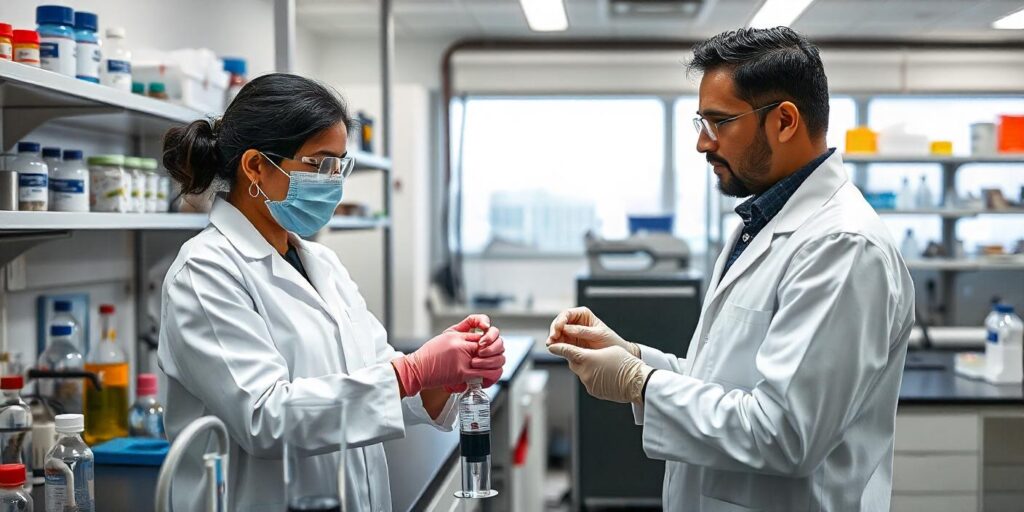
Industrial gas purity testing is a cornerstone of quality assurance, making it an indispensable practice for industries striving for excellence and compliance.
Why Is Industrial Gas Purity Testing Important?
Industrial gas purity testing is crucial for several reasons, as it ensures not only the efficiency of operations but also the safety, quality, and cost-effectiveness of industrial processes. The following expanded points delve deeper into the importance of maintaining high-quality industrial gases.
1. Ensures Product Quality
Industrial gases play a critical role in the production of high-quality goods, especially in sensitive industries like pharmaceuticals, electronics, and food processing. In these sectors, even small amounts of contaminants can compromise the integrity of the final product. For instance:
- In the pharmaceutical industry, the purity of gases used in the synthesis of drugs or in the packaging process ensures that the medications remain uncontaminated and effective.
- In electronics manufacturing, gases such as nitrogen or oxygen are used in processes like semiconductor fabrication. Impurities in these gases can affect the precision of microchips, potentially causing defects in the finished product.
- In the food industry, gases like carbon dioxide or nitrogen are used in packaging and preservation. Any impurities could lead to spoilage or contamination of food products, affecting consumer safety and brand reputation.
Testing gas purity ensures that these industries can produce consistent, reliable, and high-quality products by preventing the introduction of unwanted contaminants.
2. Enhances Safety
Certain gases, even in small quantities, can be hazardous. Impurities such as carbon monoxide (CO) in oxygen (O2) or moisture in hydrogen (H2) can present serious safety risks in industrial environments. These risks are particularly important in sectors that deal with life-critical applications, such as healthcare and welding. For example:
- In the healthcare industry, oxygen is used in medical breathing apparatus. Impurities, especially carbon monoxide, can endanger patients by interfering with oxygen transport in the bloodstream, leading to serious health issues or even death.
- In welding, gases like acetylene and oxygen are used to create the heat necessary for cutting and welding materials. Contaminants such as moisture can lead to explosive reactions, creating an unsafe work environment and risking the lives of workers.
By ensuring the purity of industrial gases, these risks are minimized, contributing to a safer working environment and protecting both workers and consumers.
3. Regulatory Compliance
Industries are governed by strict regulations that dictate the quality of gases used in production processes. Failing to meet the required gas purity standards can result in significant legal and financial repercussions. Compliance with these regulations ensures that businesses can:
- Avoid costly fines and penalties.
- Prevent operational shutdowns due to non-compliance.
- Maintain certifications and industry standards, which are often necessary for continued market access.
For instance, the FDA and EMA have specific regulations concerning the purity of gases used in the pharmaceutical and medical device industries. Similarly, ISO standards require high purity gases for industries such as aerospace and semiconductor manufacturing. Regular industrial gas purity testing is a proactive approach to meeting these regulations and ensuring seamless operations.
4. Protects Equipment
Industrial equipment, whether it’s used for manufacturing or research purposes, is designed to operate with clean, uncontaminated gases. Gases with impurities can cause corrosion or degradation of equipment over time. For example:
- Corrosion of pipelines and machinery: Moisture, oxygen, or sulfur-containing impurities can damage the internal components of pipes, valves, and machinery. This can result in expensive repairs, unplanned downtime, and a decrease in the overall lifespan of critical equipment.
- Blockages or malfunctions: Impurities like particulate matter can clog filters, valves, and other components of industrial systems. This can lead to malfunctioning of production lines or even complete system failures.
Regular purity testing ensures that the gases used are free from harmful contaminants, protecting valuable equipment and reducing the likelihood of costly repairs or replacements.
5. Optimizes Processes
Many industrial processes require high-purity gases to function efficiently. In many applications, the purity of the gas directly impacts the performance of the process:
- In laser cutting or welding, high-purity gases such as nitrogen or argon are necessary to prevent oxidation and ensure clean cuts and seams. Impurities could cause the material to oxidize, leading to reduced quality and performance.
- Cryogenic applications in industries like aerospace, medical research, and food storage require gases like liquid nitrogen at very high purity levels. Impurities could interfere with the cooling process, reducing efficiency and effectiveness in applications like cryopreservation or temperature-controlled transport.
- In chemical manufacturing, high-purity gases are essential to achieve precise reactions. The presence of contaminants can alter reaction rates, byproducts, or even cause unintended reactions, leading to inefficiencies or dangerous outcomes.
By ensuring high-purity gases, industrial processes can be optimized for better performance, efficiency, and cost-effectiveness. This, in turn, leads to improved productivity, higher yields, and more sustainable operations.
Common Methods of Industrial Gas Purity Testing
Industrial gas purity testing is essential to ensure that gases used in various applications meet the required specifications for safety, performance, and regulatory compliance. Different testing methods are employed based on the type of gas, the impurities being detected, and the specific application. Below is an expanded overview of some of the most common methods used to assess gas purity:
1. Gas Chromatography (GC)
Purpose: Gas Chromatography (GC) is a widely used analytical technique that identifies and quantifies the various components within a gas sample. The method involves separating the different chemical components in the gas mixture using a column and then detecting them through a detector.
Applications:
- GC is particularly effective for detecting trace impurities in gases, including hydrocarbons, organic compounds, and volatile organic compounds (VOCs).
- It is commonly used to test the purity of specialty gases used in critical industries like pharmaceuticals, electronics, and food packaging.
- It is also essential in ensuring the quality of gases used in analytical laboratories and scientific research.
Advantages:
- High Sensitivity: GC can detect impurities at very low concentrations (ppm or even ppb levels).
- Accuracy: Provides reliable and accurate results for complex mixtures.
- Versatility: GC can be used to analyze a wide range of gas mixtures and detect a broad spectrum of contaminants.
2. Mass Spectrometry (MS)
Purpose: Mass Spectrometry (MS) is an advanced analytical technique used to analyze the molecular composition of gases. It ionizes gas molecules, and the ions are then separated based on their mass-to-charge ratio and detected. The results provide detailed information about the molecular structure and the presence of any contaminants.
Applications:
- Ultra-High-Purity Gas Testing: MS is commonly used in industries that require extremely high purity levels, such as semiconductor manufacturing, aerospace, and pharmaceuticals.
- Complex Mixture Analysis: MS is ideal for analyzing complex gas mixtures where the types and concentrations of impurities may vary significantly.
- Environmental Testing: MS is used to analyze air quality and detect trace gases that could pose environmental or health risks.
Advantages:
- Detailed Insights: Provides highly detailed and specific information about the composition of gas samples.
- Sensitivity: Capable of detecting trace contaminants at extremely low concentrations.
- Precision: Offers highly accurate measurements, making it ideal for applications that require a high degree of precision.
3. Moisture Analyzers
Purpose: Moisture analyzers are used to measure the water content in gas samples. Water can be a harmful contaminant in many industrial processes, and its presence can significantly affect the performance and longevity of equipment.
Applications:
- Semiconductor Manufacturing: Moisture in gases like nitrogen, argon, or hydrogen can cause corrosion or damage to sensitive electronic components during the manufacturing process.
- Welding: Excess moisture in gases like oxygen or acetylene can lead to hazardous reactions, causing explosions or compromised weld quality.
- Cryogenic Applications: Gases used in cryogenics, such as liquid nitrogen, must be free of moisture to prevent ice formation, which can clog systems or affect the freezing process.
Advantages:
- Fast Results: Moisture analyzers provide quick and reliable results, which is essential for high-throughput testing in industrial settings.
- Real-Time Monitoring: Some moisture analyzers allow for continuous, real-time monitoring of moisture levels in gas systems, enabling immediate corrective action if necessary.
- Accurate Detection: Highly sensitive, moisture analyzers can detect even trace amounts of water in gases, ensuring optimal performance and safety.
4. Oxygen Analyzers
Purpose: Oxygen analyzers are devices used to measure the concentration of oxygen in a gas mixture. These analyzers are crucial for applications where the oxygen level must be controlled to maintain safety, efficiency, or regulatory compliance.
Applications:
- Medical Applications: Oxygen is a vital component in healthcare, particularly in respiratory devices like oxygen tanks and ventilators. Ensuring the purity of medical oxygen is critical for patient safety.
- Food and Beverage Packaging: In the food industry, oxygen is often removed from packaging to prevent spoilage. Oxygen analyzers help ensure that the levels of residual oxygen are within acceptable limits.
- Welding and Metal Cutting: Oxygen is used in processes like oxy-acetylene welding and cutting. Precise control of oxygen levels is essential for ensuring safety and optimal welding conditions.
Advantages:
- Safety: Oxygen analyzers help prevent hazardous situations by ensuring that oxygen levels remain within safe operating limits.
- Regulatory Compliance: Many industries are required to adhere to strict regulations regarding oxygen purity, and these analyzers help meet those requirements.
- Accuracy and Precision: Oxygen analyzers offer high accuracy, which is vital in critical applications where precise gas concentrations are necessary for safety and effectiveness.
Read More: Seal Strength Testing: Importance, Standards, Protocols, and Advanced Considerations
5. Spectroscopy Techniques
Purpose: Spectroscopy encompasses a range of techniques, such as infrared (IR), ultraviolet (UV), and Raman spectroscopy, that are used to identify and quantify the components of a gas mixture. These techniques rely on the interaction of light with the gas molecules, where different compounds absorb or scatter light at specific wavelengths.
Applications:
- Complex Gas Mixtures: Spectroscopy is ideal for analyzing complex mixtures of gases where multiple components need to be identified simultaneously. It is widely used in industrial processes where gases contain a variety of different elements or compounds.
- Environmental Monitoring: Spectroscopic methods are often used in environmental testing to monitor air quality and detect gases like CO2, methane, or nitrogen oxides.
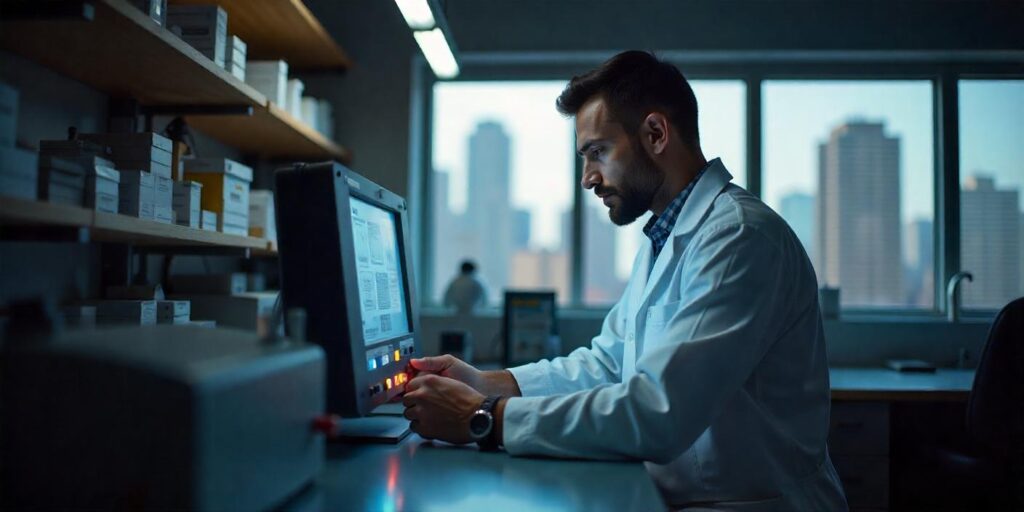
- Chemical Manufacturing: Spectroscopy can be used to monitor the purity of gases in chemical reactions or to ensure that the gas mixtures used in reactions are correct and contamination-free.
Advantages:
- Non-Destructive: Spectroscopic techniques are non-destructive, meaning the gas sample can be analyzed without altering its composition, making it ideal for valuable or limited samples.
- Real-Time Results: These techniques provide rapid, real-time analysis, allowing for immediate decision-making during industrial processes.
- Broad Application Range: Spectroscopy can be applied to a wide variety of gas types and is effective in analyzing gases with multiple components, even at trace levels.
When and Where Should Industrial Gas Purity Testing Be Conducted?
Routine Monitoring
Regular testing ensures ongoing compliance and optimal performance.
Before Critical Operations
Testing gases prior to their use in sensitive applications, such as medical or semiconductor manufacturing, prevents contamination risks.
During Production Processes
Real-time monitoring can detect deviations and allow for immediate corrective actions.
Post-Delivery Verification
Ensuring the purity of gases delivered by suppliers maintains quality and trust in the supply chain.
Incident Response
In case of a contamination event, testing identifies the root cause and prevents future occurrences.
Best Practices for Industrial Gas Purity Testing
- Understand Regulatory Requirements: Familiarize yourself with the standards applicable to your industry, such as ISO 8573 for compressed air or USP standards for medical gases.
- Use Certified Equipment: Ensure testing instruments are calibrated and maintained to guarantee accurate results.
- Implement Quality Control Protocols: Establish clear procedures for sampling, testing, and documenting results.
- Partner with Accredited Laboratories: Engage certified testing providers for reliable and credible analyses.
- Train Personnel: Educate employees on the importance of gas purity and proper handling practices.
- Adopt Real-Time Monitoring: Invest in automated systems to continuously assess gas purity during operations.
Challenges in Industrial Gas Purity Testing
- Trace Detection: Identifying extremely low levels of contaminants requires advanced equipment and expertise.
- Sample Integrity: Maintaining sample quality during collection, transport, and testing can be challenging.
- Regulatory Complexity: Adapting to evolving industry standards and regional requirements demands vigilance.
- Cost Management: Balancing the need for comprehensive testing with operational budgets is critical.
Read More:Master the A-Z of Disinfectant Efficacy Testing: Now Achieve Clean Pharmaceutical Environments
How Prewel Labs Can Help with Industrial Gas Purity Testing
At Prewel Labs, we specialize in delivering accurate and reliable industrial gas purity testing services. Here’s how we can assist:
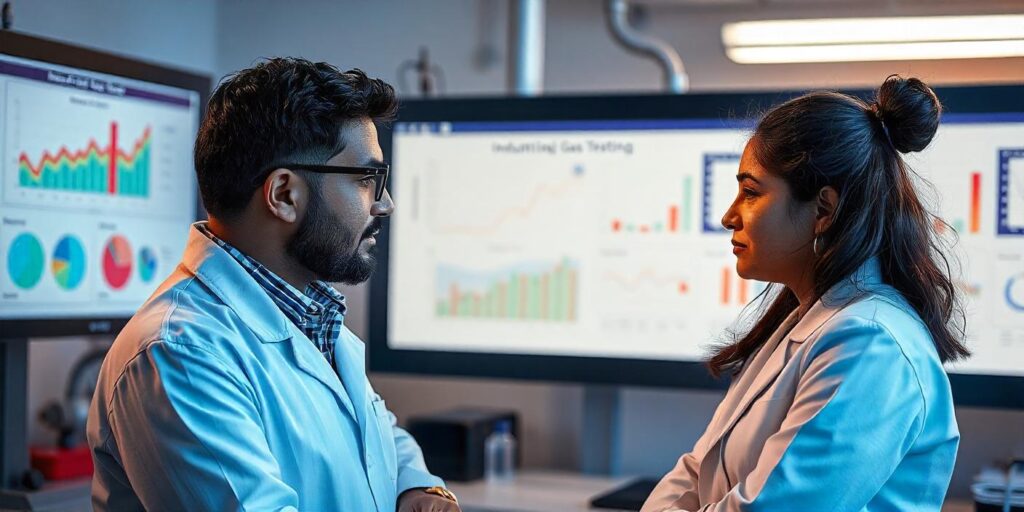
- Comprehensive Testing Solutions: We offer advanced techniques like gas chromatography, mass spectrometry, and moisture analysis to meet diverse industry needs.
- Regulatory Compliance Expertise: Our team ensures your operations align with global and regional standards, minimizing compliance risks.
- Customized Testing Programs: Tailored services based on your industry, applications, and specific gas requirements.
- Rapid Turnaround: Quick and precise testing to support your production schedules and decision-making.
- Consultation and Training: Expert guidance on implementing best practices for gas purity management and testing.
By partnering with Prewel Labs, you gain a trusted ally in maintaining the highest standards of quality, safety, and efficiency in your operations.
FAQs on the topic of industrial gas purity testing:
1. What is industrial gas purity testing?
Industrial gas purity testing refers to the process of evaluating the composition of gases used in various industrial applications to ensure they meet specific purity standards. It involves identifying and quantifying contaminants or impurities in gases like oxygen, nitrogen, hydrogen, and specialty gases.
2. Why is it important to test the purity of industrial gases?
Testing the purity of industrial gases ensures product quality, safety, regulatory compliance, equipment protection, and process optimization. Impurities in gases can compromise the performance of industrial systems, leading to safety hazards, equipment failures, and subpar product quality.
3. What are the most common methods used for industrial gas purity testing?
Common methods include Gas Chromatography (GC), Mass Spectrometry (MS), Moisture Analyzers, Oxygen Analyzers, and Spectroscopy Techniques (such as infrared, UV, and Raman spectroscopy). Each method is suited for detecting specific types of impurities and is chosen based on the gas and the contaminants involved.
4. How do Gas Chromatography and Mass Spectrometry differ in testing gas purity?
Gas Chromatography (GC) separates and quantifies components of a gas sample, making it ideal for detecting trace impurities. Mass Spectrometry (MS) analyzes the molecular composition of gases and provides detailed insights into contaminants, often at even lower detection limits, making it suitable for ultra-high-purity gas testing.
5. What types of impurities are commonly tested for in industrial gases?
Common impurities include moisture, hydrocarbons, carbon monoxide, carbon dioxide, oxygen, nitrogen, sulfur compounds, and particulates. The type of impurities depends on the specific gas and its intended application, with some impurities posing greater risks to product quality or safety.
6. How does moisture in industrial gases affect industrial processes?
Moisture in gases can cause corrosion in equipment, leading to malfunctioning or reduced lifespan of components. In sensitive applications like semiconductor manufacturing, moisture can cause defects in products. Moisture also poses a risk in processes such as welding, where it can lead to dangerous explosions or compromised weld quality.
7. What industries require strict gas purity testing?
Industries like pharmaceuticals, semiconductor manufacturing, aerospace, food and beverage packaging, healthcare, and welding rely on high-purity gases. In these sectors, impurities can directly affect product quality, safety, and performance, making regular purity testing essential.
8. How often should industrial gas purity be tested?
The frequency of gas purity testing depends on the application and the criticality of the gas. For high-purity gases or critical industries like pharmaceuticals, testing may be required on a regular basis or even continuously. For other applications, periodic testing may suffice, often aligned with operational or regulatory requirements.
9. What happens if gas purity levels fall below the required standard?
If gas purity levels fall below the required standard, it can lead to production delays, product defects, equipment damage, safety hazards, and regulatory violations. In critical industries, non-compliance can result in severe penalties, including fines, recalls, or shutdowns of production facilities.
10. Can industrial gas purity testing be automated for continuous monitoring?
Yes, many modern industrial gas purity testing methods can be automated for continuous monitoring. Devices like oxygen analyzers and moisture sensors can provide real-time data, allowing for immediate adjustments to maintain optimal gas purity levels. This is particularly important in high-throughput or mission-critical environments where constant monitoring is essential.
Conclusion
Industrial gas purity testing is more than a regulatory requirement; it’s a cornerstone of safety, quality, and operational excellence. By understanding its importance, implementing best practices, and partnering with experts like Prewel Labs, industries can ensure the highest standards of gas purity and performance. Reach out to us today to learn how we can help elevate your operations through precise and reliable industrial gas testing solutions.
Authors
-
Surendra is an Assistant Manager in the Utility Testing Department with over 8 years of experience in steam, compressed air, and industrial gas purity testing. He has worked with leading testing service providers, including SGS, and has conducted on-site testing for top manufacturing, pharmaceutical, and food & beverage industries such as Merck, Biocon, Coca-Cola, and many others. Passionate about quality and compliance, he shares technical insights to help industries maintain optimal utility standards.
View all posts -
With an abundance of experience in the field of SEO, Adithya is someone who is curious about the domain. He has published over 700 articles under his name and has worked for companies like EssentiallySports, TCS, and more.
View all posts -
Arjun Jha has over 8 years of experience in tech startups, business strategy, and digital and traditional marketing. He’s helped many startups grow by using creative strategies and a deep understanding of the market. Outside of work, Arjun enjoys reading about business, philosophy, psychology, and spirituality, which inspires his unique approach to problem-solving and growth.
View all posts