In the pharmaceutical and medical device industries, cleanroom environments are pivotal to ensuring product quality and patient safety. A cornerstone of maintaining these environments is disinfectant efficacy testing (DET), a critical process to verify that disinfectants effectively combat microbial contamination. Compliance with regulatory standards is non-negotiable, as lapses can lead to production halts, regulatory penalties, or, worse, patient harm.
This comprehensive guide details individual steps to master DET compliance, helping you stay ahead of evolving regulatory demands while optimizing your contamination control strategies.
Step 1: Conduct a Comprehensive Risk Assessment
A thorough risk assessment is the foundation of an effective Disinfectant efficacy testing program. Begin by analyzing your cleanroom’s unique environment and operational characteristics. Examine historical environmental monitoring data to identify trends in microbial contamination. Assess which microorganisms are most prevalent in your facility and determine which areas are most vulnerable.
Critical surfaces, such as equipment handles, cleanroom walls, and flooring, should be a priority. These high-contact areas often harbor contaminants that can compromise sterility. Additionally, evaluate process vulnerabilities, such as cleaning inconsistencies or poor airflow, to address potential microbial growth risks proactively.
A well-executed risk assessment not only informs disinfectant selection and testing but also strengthens your overall contamination control strategy.
Step 2: Choose the Right Disinfectants
Not all disinfectants are suitable for every environment, making the selection process a critical step in disinfectant efficacy testing compliance. Begin by considering the spectrum of activity. Your disinfectant should be effective against the bacteria, fungi, and spores most likely to be encountered in your facility.
Next, evaluate material compatibility. Ensure the disinfectant won’t corrode or degrade critical surfaces or equipment over time. A disinfectant that damages cleanroom materials can inadvertently introduce new contamination risks.
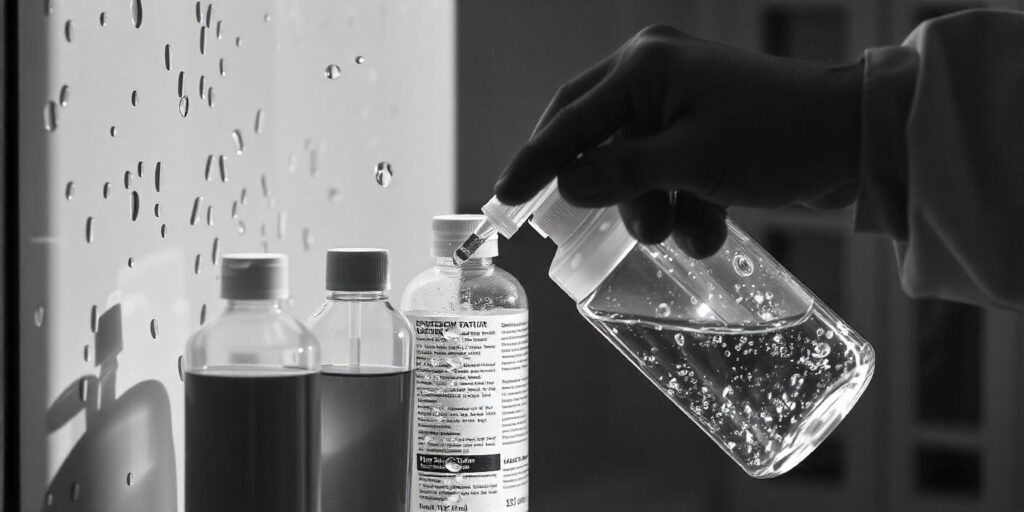
Finally, prioritize regulatory approval. Disinfectants registered with the Environmental Protection Agency (EPA) or those compliant with European Norm (EN) standards provide added assurance of efficacy. Documenting your rationale for selecting specific disinfectants demonstrates due diligence and aids in regulatory audits.
Step 3: Customize Testing Protocols
Regulatory bodies such as the FDA, EMA, and ISO expect disinfectant efficacy testing to be tailored to the specific conditions of each facility. Start by ensuring that disinfectants are tested at their in-use concentrations and contact times. Many facilities mistakenly test at ideal conditions rather than operational ones, leading to compliance gaps.
Include facility-specific surface materials in your tests. Cleanrooms often utilize stainless steel, glass, or specialized plastics, and disinfectant effectiveness can vary across these materials. Testing against microorganisms isolated from your environment rather than standard laboratory strains ensures real-world relevance and strengthens your compliance program.
By aligning testing protocols with your facility’s unique conditions, you can demonstrate that your disinfectants perform effectively where it matters most.
Read More: 7 Things to Know When You Are Choosing Your Disinfectant Efficacy Testing Partner
Step 4: Align with Regulatory Guidelines
Regulatory expectations surrounding disinfectant efficacy testing are continually evolving, making it essential to stay informed. Guidelines such as the FDA’s “Guidance for Industry on Sterile Drug Products,” the EU GMP Annex 1, and ISO 14698 provide critical benchmarks.
For instance, the revised EU GMP Annex 1 places greater emphasis on contamination control strategies, elevating the importance of disinfectant efficacy testing. Proactively aligning with such updates demonstrates your commitment to compliance and minimizes the risk of observations during inspections.
Regularly reviewing and incorporating the latest regulatory guidance helps ensure your facility remains compliant and prepared for audits.
Step 5: Partner with Qualified Laboratories for Disinfectant Efficacy Testing
Collaboration with an experienced and accredited laboratory is essential for accurate and compliant disinfectant efficacy testing results. Look for laboratories certified under ISO/IEC 17025, as this accreditation signifies adherence to rigorous quality standards.
Experience in pharmaceutical and medical device testing is also critical. Your laboratory partner should understand industry-specific requirements and offer customized testing to accommodate your facility’s isolates and surface materials. Additionally, seek labs that can provide detailed documentation and traceability, as these are vital for regulatory inspections.
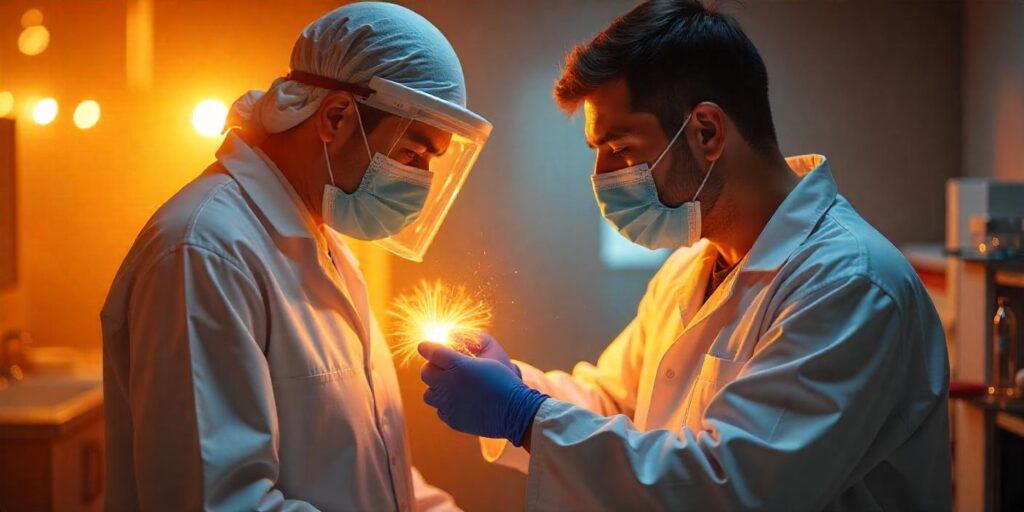
A reliable testing partner not only ensures accuracy but also supports you in addressing potential compliance challenges effectively.
Step 6: Maintain Comprehensive Documentation
Regulatory compliance hinges on thorough and accessible documentation. Inspectors will review your DET records to verify adherence to protocols. Ensure your documentation includes detailed testing procedures, results for each surface and isolate, and the lot numbers and expiration dates of the disinfectants used.
Consider adopting a digital documentation system to streamline record-keeping. Digital tools allow for real-time updates, improve traceability, and simplify audits, reducing the risk of missing critical data during inspections.
Investing in robust documentation practices safeguards your compliance efforts and enhances operational efficiency.
Read More: Debunking the Top 7 Myths in Disinfectant Efficacy Testing
Step 7: Establish a Culture of Continuous Improvement
Mastering disinfectant efficacy testing compliance requires more than meeting current standards; it demands a proactive approach to improvement. Regularly train your staff on DET protocols, emphasizing the importance of accurate and consistent testing. This not only strengthens your compliance efforts but also fosters a culture of accountability.
Leverage technological advancements, such as automated systems for environmental monitoring and disinfectant application, to enhance efficiency. Additionally, schedule periodic reviews of your DET program to identify areas for optimization. Staying ahead of regulations is easier when continuous improvement is embedded in your organization’s practices.
Step 8: Implement Routine Validation and Requalification
Compliance doesn’t end with initial testing; it requires ongoing validation and periodic requalification of disinfectants and procedures. Routine validation ensures that disinfectants remain effective under current operational conditions, which may evolve over time due to changes in processes, materials, or environmental factors.
Establish a schedule for requalification based on risk assessments and regulatory requirements. For example, disinfectants should be revalidated when introducing new equipment, materials, or cleaning procedures, or after a significant contamination event.
During validation, re-test disinfectants against updated facility-specific isolates to confirm their continued effectiveness. This step also includes reviewing cleaning protocols to identify opportunities for improvement.
Routine validation and requalification demonstrate your commitment to continuous compliance and provide an additional layer of assurance to regulators that your cleanroom practices remain state-of-the-art.
Read More: 5 New Cutting-Edge Technologies in Disinfectant Efficacy Testing
Conclusion
Mastering disinfectant efficacy testing is essential for maintaining cleanroom sterility and meeting regulatory expectations. By following these detailed steps—conducting risk assessments, selecting the right disinfectants, customizing testing protocols, staying aligned with guidelines, partnering with qualified labs, maintaining documentation, and fostering continuous improvement—you can ensure robust compliance and protect both your operations and patients.
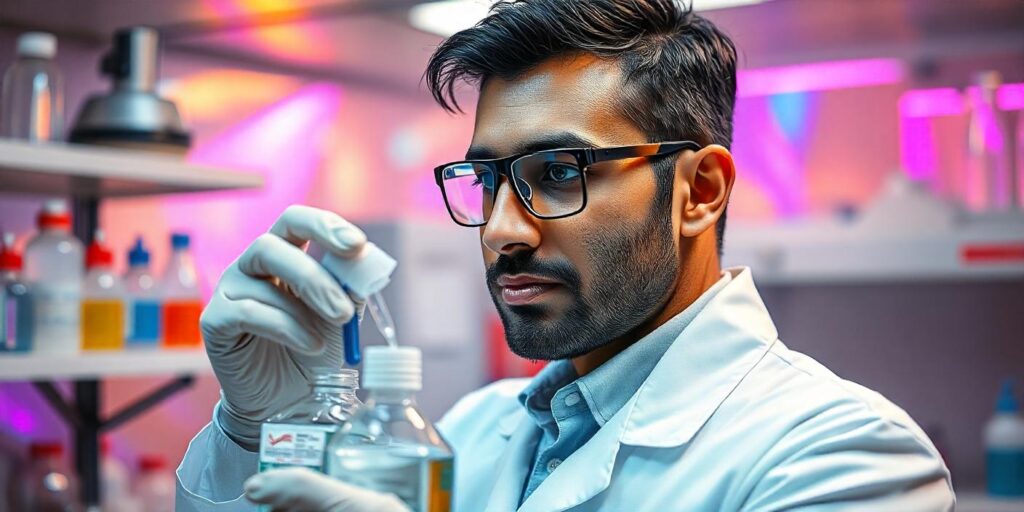
Disinfectant efficacy testing compliance isn’t just about avoiding penalties; it’s about achieving excellence in contamination control. Take the steps today to refine your practices, and position your company as a leader in cleanroom safety and regulatory adherence.
When you choose an expert like Prewel Labs as your disinfectant efficacy testing partner, you’re not just ensuring compliance—you’re building a strategic partnership with a team dedicated to your success. Our client-centric approach, cutting-edge facilities, and regulatory expertise make us the trusted choice for disinfectant efficacy testing.
Authors
-
With over 20 years of experience in the pharmaceutical sector, Kumar Swamy M V is a seasoned expert in Quality Control Microbiology. Holding a Master’s degree in Microbiology, he has built a distinguished career across notable organizations, including Syngene, Biomed, Hikal, Apotex, and Cipla. His extensive industry knowledge spans various regulatory standards, such as USFDA, MHRA, ANVISA, and WHO, making him a trusted authority in compliance and audit
View all posts -
With an abundance of experience in the field of SEO, Adithya is someone who is curious about the domain. He has published over 700 articles under his name and has worked for companies like EssentiallySports, TCS, and more.
View all posts -
Arjun Jha has over 8 years of experience in tech startups, business strategy, and digital and traditional marketing. He’s helped many startups grow by using creative strategies and a deep understanding of the market. Outside of work, Arjun enjoys reading about business, philosophy, psychology, and spirituality, which inspires his unique approach to problem-solving and growth.
View all posts